Can you Weld Rebar?
I got recently a query from a friend- Can you weld rebar? As a Welding Engineer, my answer- Why not?
This post cover all the queries related to welding rebar, welding rod selection for rebar welding, types of rebar and welder qualification for rebar welding. Welding rebar is a process that can be used to join together two pieces of rebar. This process can be used to create a variety of structures, including: buildings, bridges, and even sculptures.
Can rebar be welded?
Yes, rebar can be welded. Rebar is a steel bar or mesh of reinforcing bars used in concrete construction. It is strong enough to withstand tension and keep concrete from cracking or breaking.
Rebar are mostly made of mild steel or carbon steel material. Welding rebar together can create a stronger bond than using concrete or bolts alone. However, welding rebar requires special equipment and training.
Rebar must be cleaned before it can be welded. Otherwise, the weld will not adhere properly to the metal.
Rebar welding
If you’re a welder, there’s a good chance you’ve been asked to weld rebar at some point in your career.
A rebar, or reinforcing bar, is a common steel bar that’s used to reinforce concrete and other masonry structures. While rebar welding isn’t the most glamorous welding job, it can be very rewarding.
Read more: Rebar welding guidelines
There are two main types of rebar welding: lap welding and butt welding. Lap welding is the most common type of rebar welding, and involves overlapping two pieces of rebar and then welding them together. Butt welding is less common, but is often used when connecting shorter pieces of rebar together.
What Is Rebar?
Rebar is a common steel reinforcing bar/rod used in concrete construction. It is formed from carbon steel and is given ridges for better grip. Rebar’s surface is usually deformed to further improve its bond with the concrete.
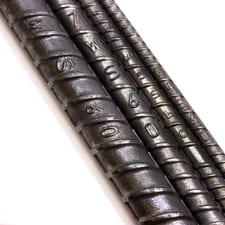
While rebar comes in different grades, the most common type used in residential construction is grade 60, which has a yield strength of 60,000 psi. This means that it can withstand up to 60,000 pounds per square inch (410 MPa) of stress before it begins to deform.
How to weld rebar?
There are several things to consider when welding rebar. The first is the type of metal being used. Rebar is usually made from either low carbon steel or medium carbon steel.
The type of metal will affect the weldability, as well as the strength and durability of the finished product.
Another important consideration is the diameter of the rebar being used. Rebar comes in a variety of sizes, ranging from small diameter rods to large diameter pipes.
The size of the rebar will determine the size and shape of the weld bead that is produced.
When welding rebar, it is important to use the correct type of electrode. Rebar is typically made from carbon steel, so an electrode that is compatible with carbon steel should be used. The most common type of electrode used for welding rebar is an E7018 electrode.
E7018 electrodes are easy to use and provide excellent results when used properly. When welding rebar, it is important to maintain a short arc length to prevent the formation of slag pockets. It is also important to keep the weld area clean and free of debris to ensure optimal results.
Welding Preheat for Rebar Welding
The high carbon content of rebar can make it difficult to achieve proper weld penetration, and the presence of rust or mill scale can further complicate matters. In addition, rebar is often welded in cramped spaces that may not be well ventilated.
Minimum preheat & Interpass temperature for rebar welding is 50 Deg F and the maximum is 500 Deg F as specified in the below table for different rebar thicknesses based on the Carbon Equivalent value.
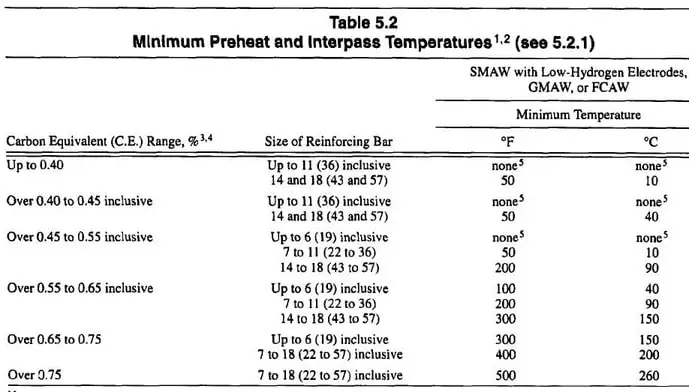
All of these factors underscore the importance of proper welding preheat. By applying heat to the rebar before welding, you can help to ensure that the steel is clean and free of contaminants. This will help to improve weld quality and prevent problems like porosity and cracking.
There are several ways to apply preheat to rebar, including using an oxy-fuel torch, electric resistance heating, or induction heating.
Welding Electrode for Rebar Welding
If you are looking for a welding electrode that is specifically designed for rebar welding, then you will want to choose a welding electrode that is made from low carbon steel.
This type of electrode is ideal for use with AC or DC power sources and can be used with either a standard or inverter-based power source.
Stick Welding Electrodes for Rebar Welding
The commonly used rebar stick welding electrodes as per AWS D1.4 are:
- E7015 (for welding of ASTM A615-Gr 40, 300, ASTM A617- Gr 40 & 300).
- E7016 (for welding of ASTM A615-Gr 40, 300, ASTM A617- Gr 40 & 300).
- E7018 (for welding of ASTM A615-Gr 40, 300, ASTM A617- Gr 40 & 300).
- E7028 (for welding of ASTM A615-Gr 40, 300, ASTM A617- Gr 40 & 300).
- E8015-X (for welding of ASTM A615-Gr 50, 350, ASTM A706- Gr 60 & 420).
- E8016-X (for welding of ASTM A615-Gr 50, 350, ASTM A706- Gr 60 & 420).
- E9015-X (for welding of ASTM A615 & 616-Gr60, 420, ASTM A617- Gr 60 & 420).
- E9016-X (for welding of ASTM A615 & 616-Gr60, 420, ASTM A617- Gr 60 & 420).
- E9018-X (for welding of ASTM A615 & 616-Gr60, 420, ASTM A617- Gr 60 & 420).
- E10018-M, E10015-X, E10016-X, E10018-X (for welding of ASTM A615 -Gr75, 520).
When welding rebar, it is important to have an electrode that has a good arc stability and can produce a strong weld bead. The low carbon steel electrodes meet these requirements and will provide you with the best results when welding rebar.
MIG Welding (GMAW) Electrodes for Rebar Welding
MIG Welding (GMAW) Electrodes for Rebar Welding are:
- ER70S-6, ER70S-2 (for welding of ASTM A615-Gr 40, 300, ASTM A617- Gr 40 & 300)
- ER80S-G (for welding of ASTM A615-Gr 50, 350, ASTM A706- Gr 60 & 420)
- ER90S-G (for welding of ASTM A615 & 616-Gr60, 420, ASTM A617- Gr 60 & 420)
FCAW Welding Electrodes for Rebar Welding
FCAW Welding Electrodes for Rebar Welding are:
- E71T1-C/ E71T1-M
- E80T1-C/ E71T1-M
- E90T-1C- E71T1-M
Why Rebar is must In Concrete?
Reinforced concrete is a combination of concrete and steel. The steel reinforcement bars, or rebar, are placed in the concrete to provide extra strength and support. Without rebar, concrete is much weaker and can crumble under heavy loads.
- Concrete can be susceptible to cracking and other forms of damage. This is why rebar is often used in concrete to reinforce it and help prevent cracking.
- Reinforced concrete is used in a variety of construction projects, from sidewalks to skyscrapers. It is especially important in buildings that experience high winds or earthquakes, as the added strength of the rebar can help prevent the structure from collapsing.
- While rebar does add strength to concrete, it is not always necessary. For small projects like sidewalks, a simple wire mesh may be all that is needed to reinforce the concrete. But for larger projects like buildings or bridges, rebar is essential to ensuring the safety of the structure.
- While rebar is not always necessary, it can be a good idea to use it in situations where concrete may be subject to high levels of stress or where it will need to support heavy loads. Rebar can make a big difference in the strength and longevity of concrete structures.
How Rebar gives Strength to the Concrete?
Rebar is an important part of reinforced concrete. It is a steel bar or mesh that is used to reinforce the concrete. The concrete is strong in compression but weak in tension. The rebar helps to hold the concrete together in both tension and compression.
without rebar, concrete is very weak and can easily crack and crumble. Rebar strengthens concrete by providing support to the structure when weight or force is applied to it.
The steel bars are placed in a grid pattern and held together with steel wire or welds. This creates a strong foundation that can support heavy loads.
Rebar is an essential part of any concrete structure, whether it’s a home foundation or a skyscraper. Without rebar, concrete would be much weaker and more prone to cracking and crumbling.
So next time you see a building under construction, take a closer look at the rebar – it’s what gives strength to the concrete.
Size & Spacing for Rebar Welding
The size and spacing of the rebar will depend on the load that will be placed on the concrete. For example, if heavy traffic will be going over the concrete, then a larger and spaced-out rebar will be needed.
As for spacing, rebar should be placed at least 2 inches apart when being welded together. This will ensure that the welds are strong and will not fail under stress.
Generally speaking, the rule of thumb for rebar welding is to have a minimum distance of 1-2 times the diameter of the rebar between each piece.
So for 16mm rebar, you would want to have a minimum spacing of 32mm between each piece.