Difference between E309L-15, 16 17, E316L-15,16 and 17 & 26
For Stick or SMAW Welding stainless steel electrodes, there are 4 types of electrode coating, like -15, -16, -17, and -26. The electrodes are designated as E309L-15, E309L-16, E309L-17, E309L-26, etc.
The same rule is applicable for other stainless steel electrodes as per AWS A5.4 aka SFA 5.4 such as E308, E316, E310, E321, and so on. So, what is the difference between these different types?
First of all, these are called, Usability characteristics of the electrode mean the factors that affect how an electrode can be used?
Get Welding Symbols Quick Card (English only)
You must remember that this number does not affect the mechanical properties or chemical properties of the electrodes. They only affect the electrical characteristics and welding positions as shown in the below table.

As you notice in the above table, the -15 designated electrode works with only DCEP polarity due to basic coating type while, -16, -17 & -26 are can be used with DCEP and AC polarity. Let us see the differences in-depth for each of these electrodes.
Usability Characteristics of SMAW/ STICK Welding Electrode
The type of covering used for an electrode core wire to make a SMAW or stick welding electrode usually determines the usability characteristics of the electrode.
This article explains the covering types which are used by the electrode manufacturers.
What is Usability Designation -15 for welding electrode?
Stainless Steel welding Electrodes (AWS A5.4 specification) with 15 NUMBER (-15 designation) at the end e.g. 309L-15 which is a lime type coating rod (Basic type) and is shall be used for DCEP polarity only.
These electrodes produce lighter welding slag compared to other 2 types (16 and 17) and are used in all welding position, while some of these rods only used for vertical downhill welding.
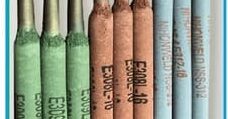
They give better impact properties compared to other types due to their basic coating. The coating of these electrodes is the basic type that is similar to the E7018 electrode. -15 designated electrodes give higher weld metal toughness compared to other types.
The electrodes having -15 designation are used with DCEP (electrode positive) only. AC polarity is sometimes used but will not produce a good result during welding.
Electrodes up to 5/32 inches or 4 mm are used in all positions while above that, they are limited in flat & horizontal position welding only.
What is the difference between ER70S-6 (ER49S-6) and ER70S-3 (ER49S-3)?
What is Usability Designation -16 for welding electrode?
Electrode with 16 number at the end e.g. 309L-16 has titania based or rutile type coating on rod. These welding rod are used with AC & DCEP polarity both.
Welding rod of 5/32 inches (4.0 millimeters) & smaller diameters are can be used for all positions welding.
Electrodes having -26 classifications is similar to -16 coating type, but give a higher deposition rate and are only used for flat & horizontal welding position compared to -16 type, and will not work for the vertical and overhead position.
The covering for -16 types rods has readily ionizing elements, such as potassium, to stabilize the welding arc with alternating current (AC polarity).
Welding rods smaller than 5/32 inches or 4.0 millimeters can be used for all positions welding.
What is Usability Designation -17 for welding electrode?
Electrode with 17 numbers at the end e.g. 309L-17 are made with silica-titania coating and it is a modified version of a -16 electrode, where small amount of titania is changed with silica. The main features of -17 type welding electrodes are:
- These rod are used with DCEP (direct current electrode positive) & AC welding polarity.
- Silicon present in the electrode increases the fluidity of weld puddle. That is beneficial for stainless steel welds which are usually have low fluidity (sluggish) in the weld puddle.
- -17 designation electrodes produces flat weld bead compare to -15 & -16 types rods.
- Welding in vertical uphill progression need more weaving during welding due to slow freezing slag in -17 electrodes.
- -17 type welding electrodes were previously designated as -16 only until 1992 but it designated different due to differences in usability characteristics.
What is Usability Designation -26 for welding electrode?
Welding rods with -26 designations are having a thicker coating and are used only for flat (1F) & horizontal fillet (2F) welding positions.
They are not useful for welding in out-of-position welding. The main aim of these electrodes is to provide a higher weld deposition rate in flat & horizontal welding positions.
They can be compared to E7024 type welding rods in their properties. The thick coating also reduces the heating effect- a common issue faced with stainless steel rods & limits their overall length. But in this case, the rods can be made in longer lengths up to 18 inches.
26-Number welding rods give similar slag formation like -16 & -17 type rod. But slag has more fluidity and slow freezing compared to the -17 type rod.
Their rod core wires are made from 304L steel or low carbon steel. The slag properties of the -26 electrode are similar to those of the -16 and -17 designations.
Due to this their coating thickness is high. In addition, they require a higher welding current due to thicker coating to melt the coating during welding. 26 number rods are used only for flat and horizontal fillet welding positions.
E316L-15 meaning
E316-15 welding rod has a lime base covering on welding rod (Basic type). Due to its basic covering type, E316L-15 can only be used for DCEP polarity.
Welding with AC and DCEN polarity will result in unstable welding arc that will disappear during turning of current curve from negative to positive on AC curve.
E316-15 welding electrode due to its basic coating provides higher toughness for weld metal compared to E316-16 or E316-17 type covering rods.
E316L-16 meaning
E316L-16 type welding rod with 16 number at the end has titania based or rutile type covering on rod. These welding rod are used with AC & DCEP polarity both.
In terms of mechanical properties, both 316L-15 or E316-16 or E316-17 are having same tensile strength, yield strength and percentage elongation.
Due to readily ionizing elements, such as potassium, E316-16 can be easily used to provide a stable welding arc with alternating current (AC polarity).
E316L-17 meaning
E316L-17 type welding rod has a silica-titania covering. This coating is a modified version of a E316L-16 rod, where small amount of titania is replaced with silica coating. The characteristics of E316L-17 welding rods are:
- E316L-17 rod is used with DCEP (direct current electrode positive) & AC welding polarity.
- Silicon present in the electrode increases the fluidity of weld puddle. That is beneficial for stainless steel welds which are usually have low fluidity (sluggish) in the weld puddle.
- E316L-17 designation electrodes produces flat weld bead compare to -15 & -16 types rods.
- Welding in vertical uphill progression need more weaving during welding due to slow freezing slag in E316L-17 electrodes.
Difference between 316L-16 and 316L-17
Both E316L-16 and E316L-17 have similar mechanical and chemical properties i.e., the weld deposit made with these rods will result in same chemical composition and tensile strength.
The difference is between their coating type that affects their usability characteristics as defined above. The weld bead of E316L-17 is flat while E316L-16 weld bead is rounded.
In term of welding polarity, both 316L-16 and 316L-17 can be used with AC & DCEP (Electrode positive) welding polarity.
316L-16 rod covering contains titania or rutile elements while in 316L-17 coating, some titania is replaced with silica for improved weld features.