The welder must not only monitor the correct weld profile, but also anticipate the impact of welding on the product designed shape. Since the fused weld metal is locally heated to 3000-5000 ⁰C during arc welding, and the rest remains cold (at ambient temperature), internal stresses arise that deform and distort the part.
“Let’s understand the main types of welding distortions & deformations that occur after welding and tell you how to avoid them.“
Such physical phenomena not only spoil the appearance of the product, but also lead to the destruction of the joints, which are under additional loading.
Let’s take a closer look at how internal stresses arise, what their types are, and what to do to prevent or eliminate them.
What is Welding Stress, Deformation & Distortion?
First, let’s define these phenomena that results in welding distortion. Welding stress is a mechanical stress that occurs in the welding area and affects the joint itself and the surrounding structure.
- Stretching;
- Compressive;
- Bending;
- Twisting.

“Welding Distortions are changes in the shape of a structure due to the influence of an internal force (stress) or a change in the structure of the material. “
Some deformations occur immediately, distorting the parameters of the product, its flatness and symmetry. Other deformations manifest themselves later in the form of changing dimensions, corrosion, and destruction of welding seams.
The simplest example of stress and strain is seen when two thin sheets of steel are joined by a one-sided welding. As a result, the product loses its flatness, as the sheets are bent and pulled together, the structure takes on a V-shape. The more seams, passages and complexity of the product, the higher the chance of internal stresses.

The degree of deformation determines the possibility of further operation of the structure. In some cases, this becomes impossible or dangerous, so welders must know the causes of these phenomena, prevent them or correct them as much as possible.
Why do stresses and distortions occur during welding?
The main cause of metal stress during welding is linear expansion from heating. As the material becomes very hot in the welding area and remains cold or slightly warm in the rest of the material, a physical impact occurs. As the weld cools down, it shrinks, pulling the welded sides of the workpiece with it, resulting in deformations.
Stress inevitably occurs when welding two different materials (dissimilar metals), such as ordinary and carbon steel, or carbon and high-alloy steel. They have different melting points and, accordingly, coefficients of thermal expansion. One material stretches the other if they are tightly joined.
Structural changes are possible when the material solidifies after the heating from welding. Its density and volume change, and the stress affects neighboring areas, causing cracks in them. These are natural consequences of the welding process, and below we will discuss how to anticipate and prevent them.
Among the side causes of stresses and deformations are the following:
- Rapid cooling of the workpiece material: Welders are in a hurry to continue working, but they can’t hold the welded parts due to the high temperature, so they dip them in a container of cold water or water them from above or apply forced air on it.
- Incorrect welding calculations: It is necessary to take into account where the metal will expand when heated and give tolerances for this.
- Assembly errors: Failure to observe the clearances indicated in the drawings, or welding without grooving the edges where necessary, leads to excessive stresses and deformation of the structure.
- Small seam spacing: If the welds are placed close together, the surface will inevitably overheat and expand and then tighten. When designing a structure, it is important to place the weld seams at a sufficient distance from adjacent joints.
- Wrong welding settings: Too high amperage, incorrectly selected electrode diameter, incorrect torch holding angle lead to overheating of parts, distorting the design parameters.
- Wrong Welding sequence: Experienced welders know that the stress of the metal can be controlled by aligning the product by alternately applying seams in different places. Without a strict sequence and alternation of heating sides, the product will simply bend in an arc.
How distortions are classified?
“As we saw earlier, based on the causes of formation, there are two types of stresses and distortions: thermal and structural. The former are associated with exposure to high temperatures and cooling, while the latter are associated with changes in the crystal lattice. Sometimes both types of stress and strain occur at the same time.“
According to the place of occurrence of stresses, they can be local (in a weld seam, joint, one section of the workpiece) or on the entire structure. For example, an improperly welded sheet metal container will turn out to be all bumpy (the walls will be wavy) or the sides will become concave.
According to the direction of deformations, there are: linear (manifest themselves only in one direction), planar (diverge in different directions along the plane) and volumetric (affect three axes of the structure).
According to the period of action, the tension can be temporary and residual. The first occurs during the welding process and goes away after the parts have cooled down. Deformations, even if they appear, also disappear, which is why they are called plastic (the metal itself takes the correct shape).
In the second case, the stress continues to act in the material even after the parts have cooled down, and the deformations from it are considered elastic.
How to Prevent Distortions & Deformation in Welding?
It is often possible to reduce or prevent the formation of deformations during welding at the design and assembly stage by providing a place for the material to shrink.
For example, a welder needs to connect two angles to maintain a center distance of exactly 500 mm (or 400, 600 mm). When assembling, lay out the parts so that the center distance is 503 mm. After welding, there will be a stress that will shrink the sides, and the width in the center of the posts will be exactly 500 mm.
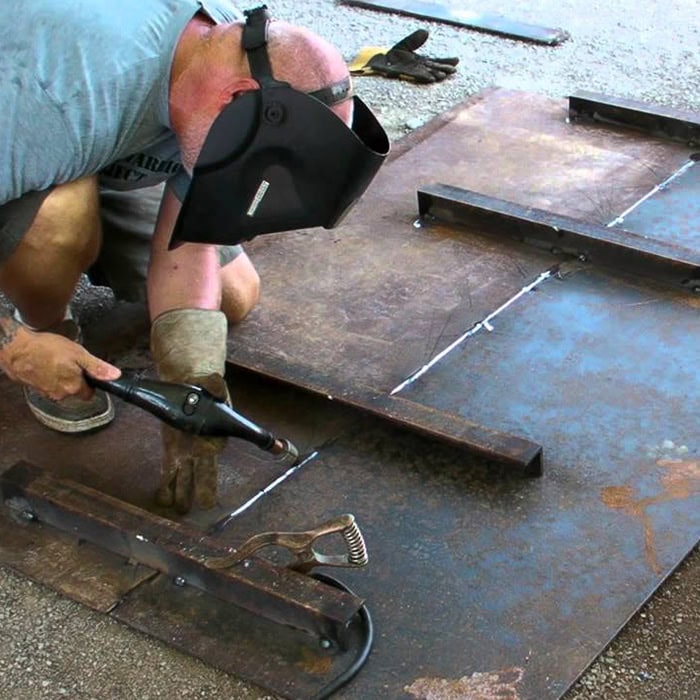
Another example of an assembly with deformation avoidance. 1-5 additional elements (pipes) need to be welded to a tubular rack with a wall thickness of 6.10 mm, but all of them will be located on the same side.
Numerous seams will first warm up this side and then tighten, inevitably arching the rack. With this in mind, initially bend it slightly to the opposite side. It is best to use a template with the possibility of fixing (pressing), where copper substrates with a thickness of 3-4 mm are placed under the lower central part of the product.
Other techniques used by welders to prevent deformation include:
- Alternate positioning of tacks on both sides to resist internal pulling forces.
- Splitting long seams into shorter seams.
- Welding of long lengths by the reverse step method.
- Reduction of the length of joints, if this does not affect the strength of the structure.
- Welding adjacent parallel seams in different directions so that the stress from them compensates for each other.
- Temperature reduction due to a decrease in amperage, intermittent arc welding or pulse welding machines (relevant for welding aluminum and thin metals).
- Reduce the number of passes, if possible.
- Fixation of workpieces and assemblies in jigs, preventing the displacement of parts during welding.
- Alternate hardfacing on each side in the case of double-sided welding.
- Reduction of heat due to the arrangement of thin sheet products on copper plates that take away heat.
Residual stress and strain control
The elimination of residual stresses so that they do not affect the joints and the entire structure is most effectively done by annealing. The product is placed in a furnace, chamber or connected to an induction heating source, and brought to a temperature of 550-680 ⁰C. For products made of thick-walled materials, a certain annealing time (from several minutes to several hours) is provided in order to heat the structure sufficiently. The product is then allowed to cool slowly with the oven.
This can take a day or more, but only in this case the stresses in the high-strength steel are completely relieved. If this is not done, the internal tension will come out, destroying the suture or the suture area.
Sometimes local heating of the product is enough to relieve stress. This is done by gas burners or hand torches connected to propane and oxygen tanks. A temperature of 800 ⁰C and a slight pressure on the cold edge of the structure to give the correct position are acceptable. With tubular hollow elements, you should be especially careful not to spoil the circumference by flattening the cylindrical part.
The resulting permanent deformations are eliminated by the mechanical action created by the pressure. For large thick parts, hydraulic equipment (press, rods) is used. Small thin-sheet structures are corrected by blows of rubber mallets so as not to leave dents on the surface of the metal. The impact should be reversed.
Another method of eliminating deformations by mechanical means is rolling the material, or rolling. Suitable for sheet and flat products. Thanks to the system of rollers and rollers, the structure bends in the opposite direction.