How to Save Argon Shielding Gas in Welding?
Argon shielding gas is the most commonly used gas in welding to protect the weld pool from oxidation and other atmospheric gases (nitrogen, oxygen, etc.) that can contaminate the weld. However, Argon gas is an expensive gas, so it is important to use it efficiently to save on costs.
So, It is important to ensure that the welding process is completed efficiently and with minimal gas waste. One way to achieve this cost-efficiency of welding is to save argon shielding gas in welding.
In this article, I have covered the most important tips and methods to save argon welding gas.
How to reduce the costs and save Argon Shielding Gas in Welding?
Welding is a major part of many industrial and manufacturing processes, and therefore the cost of the welding materials can be significant, especially the costly welding shielding gases.
One way to help reduce costs for complete welding is to save argon gas, which protects welds from impurities and helps produce strong sound welds with a superior appearance.

Here are some tips on how to save Argon shielding gas in welding:
1. Check for leaks
First and most important is to check for leaks in the gas lines and fittings regularly. Even small leaks can waste large amounts of Argon gas over time as welding uses continuous gas, so it is important to fix any leaks as soon as possible.
Checking for leaks in cylinders and gas lines is an important step in ensuring the safe and efficient use of Argon gas in welding.
Here are some methods for leak checking in cylinders and Argon gas lines:
A. Visual inspection
The first step in leak checking is to visually inspect the cylinder and gas lines for any signs of damage or wear.
Look for cracks, dents, or other visible signs of damage that may indicate a leak. Also, check the fittings and valves for any signs of wear or damage.
B. Soap solution
One of the most common methods for leak checking is using a soap solution. This involves mixing water with a small amount of liquid soap and then applying the solution to the fittings and valves.
If there is a leak, bubbles will form at the location of the leak. This method is easy and inexpensive, but may not detect small leaks.
Related reading: Advantages of using a gas lens in TIG Welding
C. Electronic leak detectors
Electronic leak detectors are another option for leak checking in cylinders and gas lines.
These devices use sensors to detect the presence of Argon gas and can identify even very small leaks. They are more sensitive than soap solutions and can be used to pinpoint the location of a leak.
D. Pressure drop testing
Pressure drop testing involves pressurizing the gas lines and then monitoring the pressure to see if it drops over time.
If there is a leak, the pressure will drop more quickly than expected. This method is not as accurate as electronic leak detectors or ultrasonic leak detection, but can be useful for detecting larger leaks.
2. Adjust the flow rate
The flow rate of Argon gas can also be adjusted to save on costs. If the flow rate is too high, it can waste gas and increase costs. Adjust the flow rate to the minimum required to maintain an effective shield around the weld.
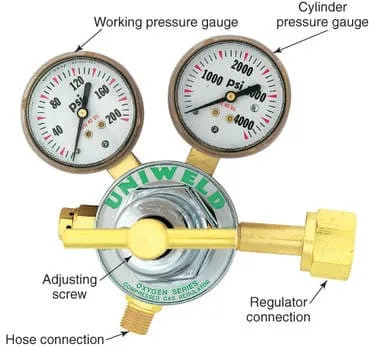
Adjusting the flow rate of Argon gas is one of the easiest and most effective ways to save on Argon gas usage in welding.
Related Reading: Right Gas Pressure for MIG welding: Find it out.
Here are some methods to adjust the flow rate and save Argon gas:
A. Check the manufacturer’s recommendations
The first step in adjusting the flow rate is to check the manufacturer’s recommendations for the specific welding process and material being used.
The recommended flow rate will depend on factors such as the type and thickness of the material being welded and the welding process being used.
B. Use a flow meter
A flow meter is a device that measures the flow rate of Argon gas. Using a flow meter can help to ensure that the flow rate is adjusted to the correct level.
This is especially important when using different welding processes or materials that require different flow rates.
C. Use a regulator
A regulator is a device that controls the pressure and flow of Argon gas. Using a regulator can help to ensure that the flow rate is consistent and adjusted to the correct level.
It is important to regularly check the regulator to ensure that it is functioning properly.
D. Minimize gas wastage
Minimizing gas wastage is another important factor in saving Argon gas. This can be done by using a nozzle that is the right size for the job, keeping the nozzle close to the weld, and using a back purge when necessary.
3. Keep the nozzle close to the weld
When welding, it is important to keep the nozzle as close to the weld as possible. This helps to reduce the amount of gas required to maintain an effective shield.
If the nozzle is too far away from the weld, more gas will be required to maintain a proper shield.
4. Use the right size nozzle
The size of the nozzle used during welding affects the amount of gas used. A larger nozzle will require more Argon gas to maintain an effective shield around the weld. Therefore, it is important to use the right size nozzle for the job.
Related reading: Welding Gases Bottle Conversion Formula
5. Use a back purge
In some cases, it may be necessary to use a back purge to save on Argon gas. A back purge is a technique that involves using a separate gas source to purge the inside of a pipe or other enclosed space before welding.
This helps to reduce the amount of Argon gas required to maintain an effective shield.
6. Practice good welding technique
Finally, practicing good welding technique can help to reduce the amount of Argon gas used.
This includes minimizing the number of starts and stops during welding, using the correct welding technique for the specific material being welded, and avoiding unnecessary pauses or delays during welding.
How to Optimize and Save Argon Gas Shielding Gas?
Argon gas is an important component in welding and is used as a shielding gas to protect the weld from oxidation and other impurities.
However, Argon gas can be expensive, and optimizing its use can help to save on costs. Here are some ways to optimize and save Argon gas shielding:
Monitor gas flow during welding
One of the most important ways to optimize Argon gas use is to monitor gas flow during welding.
This can be done by using a flow meter or by visually monitoring the gas flow gauge. By keeping the gas flow at the right level, welders can ensure that they are using the minimum amount of Argon gas required for the job.
Use the gas preflow feature in the machine
Many welding machines have a gas preflow feature that allows the gas to flow for a short period of time before welding begins.
This helps to purge the air from the gas line and nozzle, ensuring that only pure Argon gas is used during welding. By using this feature, welders can ensure that they are not wasting gas during the pre-welding stage.
Regular inspection of gas lines and regulators
Regular inspection of gas lines and regulators is another important way to optimize Argon gas use.
This includes checking for leaks, inspecting the fittings and valves, and ensuring that the gas lines and regulators are functioning properly.
By keeping the gas lines and regulators in good condition, welders can ensure that they are not wasting gas due to leaks or other issues.
Related reading: Why Does Ice Form on Gas Bottles and Welding Regulators
Conclusion
In conclusion, using Argon shielding gas efficiently can help to reduce costs and save money in welding.
By using the right size nozzle, adjusting the flow rate, keeping the nozzle close to the weld, using a back purge when necessary, and checking for leaks regularly, welders can save on Argon gas costs without compromising the quality of their work.