What is Low Hydrogen Electrode?
Low-hydrogen electrode, as the name implies, are those in which the coatings are absolutely free from organic and water-bearing compounds or any other ingredients which can be a source of hydrogen.
Even the electrodes are finally baked at a temperature between 350-425° C to remove the last traces of moisture adhering to the silicate binder. A low hydrogen electrode is used in arc welding and other applications where a low-hydrogen content is desired.
Low hydrogen electrodes are made of materials that have a low affinity for hydrogen. The use of low hydrogen electrodes can help to prevent weld metal cracking.
How can you identify a low hydrogen electrode?
To identify a low hydrogen electrode, you can look for specific markings or classifications on the electrode packaging. Here’s how you can identify a low hydrogen electrode:
- AWS Classification: The American Welding Society (AWS) provides a classification system for welding electrodes. Low hydrogen electrodes are typically designated with the letter “H” in their classification code. For example, electrodes classified as “E7018-H4R” or “E7016-H8” are low hydrogen electrodes.
- “Low Hydrogen” or “Low Moisture” Labeling: The packaging or labeling of the electrode may explicitly state that it is a low hydrogen electrode. Look for phrases such as “Low Hydrogen,” “Low Moisture,” or “Low H.”
- Manufacturer’s Information: The manufacturer’s information on the electrode packaging or accompanying documentation may indicate that the electrode is designed for low hydrogen applications. This information can include statements about the electrode’s moisture resistance or low hydrogen characteristics.
- Storage and Handling Instructions: Low hydrogen electrodes require specific storage and handling procedures to maintain their low hydrogen content. The packaging or instructions may provide guidelines for proper storage conditions, such as keeping the electrodes in a dry environment or using dedicated electrode storage ovens.
Low hydrogen electrodes can be identified by their markings, which usually include “H4”. Also, welding electrodes with designation 7015, 7016 and 7018 or with last digits as “18” are low hydrogen electrodes only.
The packaging may also mention “low hydrogen” or have a distinctive color coding. The material used in the electrode coating can also be a clue, as low hydrogen electrodes often use coatings made of iron oxide or basic oxides, which are less prone to absorbing hydrogen.
low hydrogen electrode list
There are many different types of low hydrogen electrodes available, so it is important to find the one that best suits your application. The most popular type of low hydrogen electrode is the E7018, which is ideal for use in high-strength steels and alloys.

The mostly used Low hydrogen electrodes are:
- E7015
- E7016
- E7018
- E7028
- E7048
- E6018
- E8018
Rod designation | Covering type | weld positions | welding polarity |
---|---|---|---|
E7015 | Low hydrogen sodium | Flat, vertical, OH & Horizontal | DCEP |
E7016 | Low hydrogen potassium | Flat, vertical, OH & Horizontal |
DCEP, AC |
E7018 | Low hydrogen potassium with added iron powder | Flat, vertical, OH & Horizontal |
DCEP, AC |
E6018 | Low hydrogen potassium with added iron powder | Flat, vertical, OH & Horizontal |
DCEP, AC |
E7028 | Low hydrogen potassium with added iron powder | Flat & Horizontal-F |
DCEP, AC |
E7048 | Low hydrogen potassium with added iron powder | Flat, vertical, OH & Horizontal | DCEP, AC |
E8018-XX | Low-hydrogen potassium with added iron powder | Flat, vertical, OH & Horizontal | DCEP, AC |
E7015 low hydrogen sodium
E7015 electrodes are low-hydrogen electrodes to be used with direct current, reverse polarity. Their slag is chemically basic.
E7015 electrodes are commonly used for making small welds on heavy sections, since they are less susceptible to cracking. They are also used for welding high sulphur and enameling steels.
The arc of E7015 electrodes is moderately penetrating. The slag is heavy, friable, and easy to remove. The weld beads are convex, although fillet welds may be flat. E7015 electrodes are used in all positions up to 4 mm size.
Larger electrodes are used for groove welds in the flat position and fillet welds in the horizontal and flat positions. Amperages for E7015 electrodes are higher than those used with E6010 electrodes of the same diameter.
The shortest possible arc should be maintained for best results with E7015 electrodes. This reduces the risk of porosity. The necessity for preheat is reduced; therefore, better welding conditions are provided.
E7016 low hydrogen potassium
E7016 electrodes have all the characteristics of E7015 electrodes plus the ability to operate on AC.
The core wire and coverings are very similar to those of E7015, except for the use of a potassium silicate binder or other potassium salts in the coverings to facilitate their use with AC.
Most of the preceding discussion on E7015 electrodes applies equally well to the E7016 electrodes.
E7018 low hydrogen potassium, iron powder
E7018 electrode coverings are similar to E7015 coverings except for the addition of a high percentage of iron powder.
The coverings on these electrodes are slightly thicker than those of the E7015 and E7016 electrodes. The iron powder in the coverings usually amounts to between 25 and 40% of the covering weight.
E7018 low-hydrogen electrodes can be used with either AC or DC, reverse polarity. They are designed for the same applications as the E7015 electrodes.
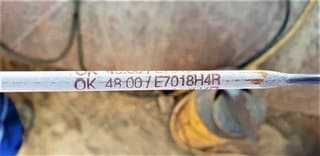
As is common with all low-hydrogen electrodes, a short arc should be maintained at all times. In addition to their use on carbon steel, the E7018 electrodes are also used for dissimilar joints involving high-strength, high carbon, or alloy steels.
The fillet welds made in the horizontal and flat positions are slightly convex in profile, with a smooth and finely rippled surface. The electrodes are characterized by a smooth, quiet arc, very low spatter, adequate penetration, and can be used at high travel speeds.
E7018-1 low hydrogen potassium, iron powder
Electrodes identified as E7018-1 have the same usability and design characteristics as E7018 electrodes, except that their manganese content is set at the high end of the range.
They are intended for use in situations requiring a lower transition temperature than is normally available from E7018 electrodes when used out of position or with high-heat input.
E7048 low hydrogen potassium, iron powder
Electrodes of the E7048 classification have the same usability, composition, and design characteristics as E7018 electrodes, except that E7048 electrodes are specifically designed for exceptionally good vertical-down welding.
E7028 low hydrogen potassium, iron powder
E7028 electrodes are very much like the E7018 electrodes. They differ as follows: the slag system of E7028 electrodes is similar to that of E7016 electrodes, rather than E7018 electrodes.
E7028 electrodes are suitable for horizontal fillet and flat welding only, whereas E7018 electrodes are suitable for all positions.
The E7028 electrode coverings are much thicker. They make up approximately 50% of the weight of the electrodes. The iron content of E7028 electrodes is higher (approximately 50% of the weight of the coverings).
Consequently, on horizontal fillet and flat position welds, E7028 electrodes give a higher deposition rate than the E7018 electrodes for any given size of electrode.
low hydrogen electrode classification
Low hydrogen electrodes classification is provided by the AWS in AWS A5.1 & AWS A5.5 .
These classifications are also covered in ASME Section IIC SFA 5.1 and SFA 5.5. Following are the main low hydrogen electrode classification used:
- E6018: AWS A 5.1
- E7015: AWS A 5.1
- E7016: AWS A 5.1
- E7018: AWS A 5.1
- E7028: AWS A 5.1
- E7048: AWS A 5.1
- E8018-XX: AWS A 5.5
low hydrogen electrode designation
A low hydrogen electrode designation is a welding electrode that has a low hydrogen content. This type of electrode is used for welding metals that are prone to hydrogen embrittlement, such as low alloy steel and carbon steel.
Low hydrogen electrodes are available in a variety of sizes and shapes, and they can be used with either AC or DC power sources.
Most commonly used low hydrogen electrode designation are:
- E6018: AWS A 5.1
- E7015: AWS A 5.1
- E7016: AWS A 5.1
- E7018: AWS A 5.1
- E7028: AWS A 5.1
- E7048: AWS A 5.1
- E8018-XX: AWS A 5.5
Low hydrogen electrode uses
When it comes to welding, using the right electrode is critical to a successful weld. For many applications, a low hydrogen electrode is the best choice. Here are some of the advantages of using a low hydrogen electrode:
1. Low hydrogen electrodes produce less hydrogen gas than other types of electrodes. This is important because too much hydrogen gas can cause porosity in the weld, which can weaken it.
2. Low hydrogen electrodes are less likely to cause cracking in the weld area. A low hydrogen electrode is an electrode used in welding that has a lower content of hydrogen than other types of electrodes.

3. Low hydrogen electrodes can be used on a variety of materials, including mild steel, carbon steel, cast steel and low alloy steel. This makes them versatile and ideal for many different applications.
4. Low hydrogen electrodes provide excellent arc stability, which results in a smoother, more consistent weld bead.
5. Low hydrogen electrodes added with iron powder provided improved weld deposition features and enhance productivity.
6. 7015 low hydrogen electrode has better penetration properties making it ideal for pipeline welding applications.
7. 7018 low hydrogen electrode having basic coating and thus provide very good toughness properties of weldment.
Low hydrogen rod covering
This contains calcium carbonate, fluoride (CaF₂), metal powders and comparatively more powerful deoxidizers, and sometimes small amounts of alumino-silicates. Moisture is completely removed from the coating to render it low-hydrogen.
The molten metal produced in the arc is well-deoxidized, killed and low in hydrogen. Therefore, as stated earlier, the metal transfer is in comparatively large droplets.
If, however, the electrodes are not thoroughly dried and have moisture in the coating, the metal transfer tends to be of the spray type.
Following are main constitutes of 7018 welding rod covering (excluding iron and alloying elements):
- Limestone (main constitute, 5- 10% of coating)
- Calcium Fluoride (5-10% of coating)
- Potassium silicate (5-10% of coating)
- Sodium Silicate (1-15% of coating)
- Titanium dioxide (1-15% of coating)
- Magnesite (less than 1% of coating)
- Lithium Silicate (less than 1% of coating)
- Hydroxyethyl cellulose (less than 1% of coating)
- Aluminum oxide (less than 1% of coating)
Determination of Hydrogen in Weld Deposit
The total hydrogen present in the weld joint after welding is the sum of two distinct fractions:
- the diffusible hydrogen and the
- residual hydrogen.
The former fraction escapes from solid metal at or near room temperature and diffuses to the surface. The latter fraction does not diffuse, but remains within the structure of the solid metal.
The method of determining diffusible hydrogen in a weld deposit has been detailed in ISO 3690, “Determination of hydrogen in weld metal arising from the use of covered electrodes for welding mild and low-alloy steels”, and reproduced in the Appendices of BS:639.
The principle of the method is as follows: A single weld bead from an electrode test is deposited on a test plate and rapidly quenched.
The specimen so produced is maintained at room temperature for 72 hours to release its content of diffusible hydrogen, which is collected over mercury and measured volumetrically. If the test has to be delayed, the test plate is stored at -78° C or lower until required for preparation and analysis.
Following materials are required:
a) Test piece assembly prepared from semi-killed steel having 0.20% maximum carbon and 0.05% maximum Sulphur. These must be degassed at 650° C for 1 hour.
b) Electrode of 4 mm size in the case of normal type and of 3.15 mm size in the case of iron powder type having deposition efficiency higher than 130%. It must be dried at 250° C for two hours.
c) A copper jig as shown in Fig. 3.16 for aligning and clamping the test piece.
d) Hydrogen collecting apparatus. A typical gas burette for the measurement of cold extracted gas is shown in Fig. 3.17. It fulfils the following requirements:
i) Mercury is used as the confining liquid.