Types of Gears
Gears are a fascinating and essential component of everyday life. From the gears in our cars to the ones used in airplanes, they play an integral role in our lives. They come in a multitude of shapes, sizes, and types; all with their own unique purpose and function. This article will focus on the various types of gears and how they are used to drive movement in machines from small gadgets to massive industrial machines.
Gears are a fundamental element of many machines and mechanisms. They provide the mechanical advantage needed to transmit force and motion between two different points. Though there are many types of gears, each with its own specific purpose, all of them share basic features: teeth that interlock, allowing one gear to drive or be driven by another.
Gears are found in a variety of applications, from automotive engines to clocks and other everyday items. There is no single type of gear that is suitable for every application; instead, there are several different types of gears designed for various purposes.
What are Gears?
Gearing is a three-link mechanism in which two moving links are gears, or wheel and rail with teeth forming with fixed by the link (body) of a rotary or translational pair.
The gear consists of two the wheels by which they interlock. Gear wheel with a smaller the number of teeth is called a gear, with a large number of teeth – a wheel.
Gears are mechanical devices consisting of a series of teeth or cogs that mesh with each other to transmit rotational motion and torque from one shaft to another.
Gears are mechanical components that transmit power and motion between rotating shafts. They are used to control the speed and torque of a rotating shaft, and to change the direction of rotation.
They are used in a wide variety of applications, including automobiles, bicycles, and industrial machinery, to change the speed or direction of rotation, increase or decrease torque, and convert rotary motion into linear motion.
They can also be used in a wide variety of other applications, such as robotics, aerospace, and industrial equipment.
Advantages of Gears
Gears main advantages are:
- Increased torque: Gears can transmit power through a mechanical advantage, allowing for increased torque output.
- Speed reduction or increase: Gears can also be used to change the speed of a rotating shaft, allowing for speed reduction or increase.
- Precision: Gears can be made to precise tolerances, which allows for precise and accurate movement in machines.
- Durability: Gears are durable and can withstand high loads and stresses.
- Versatility: Gears can be used in a wide variety of applications and machines, such as automobiles, industrial equipment, and household appliances.
- Better control: Gears help in controlling speed, direction and torque while transmitting power.
Disadvantages of Gears
Like everything else, Gears too have several disadvantages, including:
- Complexity: Gears can be complex to design, manufacture, and maintain.
- Noise: Gears can produce noise when they are in operation, which can be a problem in some applications.
- Wear and tear: Gears are subject to wear and tear, and will eventually need to be replaced.
- Lubrication: Gears require regular lubrication to function properly, which can be a problem in certain environments or applications.
- Cost: Gears can be expensive to manufacture, especially if precise tolerances are required.
- Efficiency loss: Gears can cause loss of efficiency due to friction and energy loss, which is proportional to the number of gears in a gear train.
- Limited speed range: Gears are not suitable for high-speed applications, as they can fail or wear out quickly at high speeds.
Main characteristics of the gears:
Power P1 at the input and P2 at the output, W; Power may be expressed in terms of the circumferential force Ft (H) and the circumferential velocity V (m/s) of the wheel, pulley, drum, etc.:
P = Ft×V;
speed expressed by the speed n1 at the input and n2 at the output, min–1, or by the angular velocities ω1 and ω2, c−1;
Gear ratio – angular velocity ratio Leading link to angular velocity of the driven link:

at u > 1, n1 > n2 – reduction gear, or gearbox,
at u < 1, n1 < n2 – upshift gear, or multiplier;
coefficient of efficiency (KPA)

where Pr – power lost in transmission.
Single-stage transmissions have the following efficiencies: friction – 0,85… 0,9; belt – 0,90… 0,95; toothed – 0,95… 0,99; worm – 0,7… 0,9; chain – 0,92… 0,95;
moments on the shafts. Torques T1 (N·m) on the drive and T2 on the driven shafts determined by power (kW) and rotational speed (rpm) or angular velocity (p-1):

where ω1 = ℼη1/30
Torque relationship on the drive T1 and the driven T2 shafts is expressed Via gear ratio u and efficiency η:
T2 = T1 η u.
Different types of Gears and their Uses
Gears are an integral component of many mechanical systems and are used in a variety of applications. Gears enable machines to move, convert speed and torque, and even increase efficiency. With the right gearing setup, almost any desired motion can be achieved.
Gears can be classified according to their shape, the number of teeth, and the direction of rotation, among other factors.
In this article, we will look at the different kinds of gears available, as well as some examples of how they are used in everyday life.
Spur Gear
Spur gears are the most basic and most common type of gear. They have straight teeth that are parallel to the axis of rotation. They are most commonly used in lower torque, higher speed applications.
They are relatively easy to manufacture, relatively inexpensive and they have simple geometry that makes them easy to analyze and design.

They are used in automobiles, industrial equipment, household appliances, and various other machines. They are also used in gear trains as idler gears to transfer motion between other gears.
Due to their simple design, they have high efficiency and low noise level, but their accuracy is limited. They are typically used in systems that require low-to-medium torque and high-speed applications.
Bevel Gear
A bevel gear is a type of gear that has teeth cut on a conical surface, allowing for the transmission of power and motion between intersecting axes. The bevel gear can be either straight, spiral or hypoid.
Bevel gears are commonly used in applications where the axis of rotation needs to change direction, such as in automobiles (differential gears) and industrial equipment.

Types of Bevel Gears
- Straight Bevel Gears: These are the simplest form of bevel gears and have straight teeth cut on a conical surface. They are most commonly used in low-power applications.
- Spiral Bevel Gears: These gears have helical teeth cut on a conical surface, which allows for smoother operation and less noise compared to straight bevel gears. They are commonly used in high-power applications.
- Hypoid Bevel Gears: These gears are similar to spiral bevel gears, but the shafts are not parallel, allowing for a larger gear ratio in a smaller space. They are commonly used in automotive applications.

- Zerol Bevel Gear: These gears are similar to straight bevel gears, but have curved teeth. They are typically used in high-speed, high-precision applications.
- Face Gear: These gears are similar to bevel gears, but the gear teeth are cut on a flat face rather than a cone. They are typically used in applications where space is limited.

Worm Gear
Worm gear is used to transfer rotation from one shaft to the other, when the axes of the shafts are crossed. The angle of intersection in most of cases is 90º. The most common worm transmission (Figure below) consists of the so-called Archimedean worm, i.e. a screw having trapezoidal thread with a profile angle in the axial cross-section equal to a double angle engagement (2α = 40°), and worm wheel.
A worm gear is a type of gear that consists of a worm (a shaft with a spiral thread) that meshes with a worm gear (a gear with teeth cut in the shape of a helix). The worm gear is usually a spur gear with teeth cut at a 90-degree angle to the gear’s face.
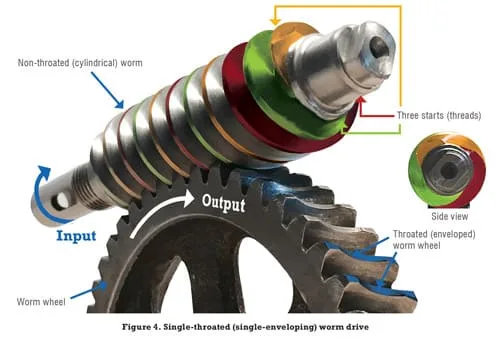
The main benefit of using worm gears over other types of gearing is their ability to transmit power at various speeds, as well as their quiet operation and low backlash.
Additionally, the meshing teeth on these components help provide self-locking action and smooth running while eliminating any need for lubrication between the two shafts – which reduces maintenance costs.
Rack and Pinion Gear
A rack and pinion gear is a type of linear actuator that uses a rotating gear (the pinion) to convert rotational motion into linear motion.
It consists of a linear flat gear bar (called rack) that has teeth cut along one edge and a circular gear (the pinion) that meshes with the teeth of the rack. The rack is typically a flat or slightly curved piece of metal or plastic that moves in a straight line, while the pinion is a small, circular gear that rotates.

When the pinion turns it moves along the length of the rack, creating straight-line motion and providing precise control for various applications.
Rack and pinion gears are widely used in industry for devices such as elevators, conveyors, power steering systems, robotics arms and many other machines where accurate positioning is needed.
Helical Gears
Helical gears are similar to spur gears, but the teeth are cut at an angle, resulting in a smoother operation and less noise. This is because the teeth engage gradually as opposed to all at once, as with spur gears.
Helical gears are a type of gear mechanism used to transfer power between rotating shafts. They have rounded teeth that interact in a helical pattern, allowing them to rotate smoothly and efficiently.

Helical gears provide smooth motion due to their curved teeth which mesh together more gradually than with other types of gear mechanisms. This reduces vibration and noise levels as well as wear on the parts themselves.
In addition to this, helical gears can also operate at much higher speeds than other types of gearing systems due to their increased efficiency when transferring power from one shaft to another.
They also offer greater strength and durability compared to spur or beveled-gear designs, making them suitable for use in heavy-duty applications such as industrial machinery and automotive components.
Crown Gear
A crown gear, also called a pinion gear, is a type of bevel gear that has teeth that are cut in a circular pattern around the gear’s perimeter. It has straight teeth, and each tooth is cut in a shape resembling the crown of a king.
The teeth of a crown gear are typically cut at a 45-degree angle, and it typically meshes with another bevel gear, such as a straight or spiral bevel gear.
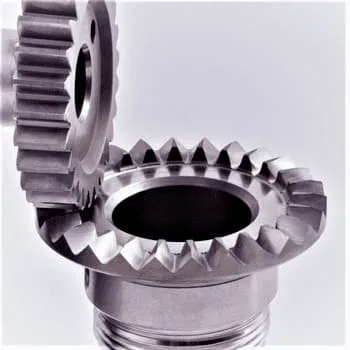
Crown gears are typically used in applications where the axis of rotation needs to change direction, such as in automobiles, industrial equipment, and construction machinery.
The design of a crown gear involves cutting cogs into one another, forming an internal meshing system that allows for smooth operation without any friction or wear-and-tear on the component parts. The unique design also enables this type of gear to be able to utilize all kinds of power sources from manual labor to electricity and energy from motors.
Herringbone Gear
A herringbone gear is a type of double helical gear, which is made up of two helical gears that are mirror images of each other and are stacked on top of each other.
The teeth of a herringbone gear are cut in a V-shape, with one side of the V pointing in one direction and the other side pointing in the opposite direction. This allows for smoother operation and less noise compared to single helical gears.

The unique design of Herringbone Gear allows for smoother operation, increased power output and improved efficiency over standard gears. The two helical teeth on each side of the gear are angled in opposite directions, meaning they mesh more efficiently than traditional designs.
This leads to less wear and tear on the gear system components, which means less maintenance and longer life span for the entire system.
Screw Gear
A screw gear is a type of gear that combines the principles of a screw and a gear. It consists of a helical gear that meshes with a screw thread, which allows for the conversion of rotational motion into linear motion. They are also known as worm screw or worm gear screw.

The most commonly used types of screw gears are helical and double-enveloping worm gears.
Helical screw gears offer a high level of efficiency while double-enveloping worm gears provide perfect meshing between the two components due to their unique shape.
These features make them ideal for use in precision machinery such as robots or CNC machines where accuracy is essential.
Gears Terminology
Gears terminology refers to the specialized vocabulary and technical terms used in the field of gears and gear systems.

These terms are used to describe the different components and characteristics of gears, such as size, shape, and function.
- Pitch: The distance between the corresponding points of consecutive teeth on a gear, measured along the pitch circle.
- Pitch Circle: The imaginary circle that is equidistant from the tops of the gear teeth. The pitch circle is used to determine the gear’s pitch and to calculate the size and position of the gear’s teeth.
- Pitch Diameter: The diameter of the pitch circle.
- Addendum: The radial distance between the pitch circle and the top of the gear teeth.
- Dedendum: The radial distance between the pitch circle and the bottom of the gear teeth.
- Tooth Face: The surface of the gear tooth that makes contact with the mating gear.
- Tooth Flank: The surface of the gear tooth that is adjacent to the tooth face.
- Backlash: The amount of clearance between the meshing gears.
- Root Diameter: The diameter of the base of the gear tooth, where it meets the gear’s hub.
- Pressure Angle: The angle between the line of action and a line perpendicular to the gear’s axis.
- Module: A measure of the size of a gear, equal to the pitch diameter divided by the number of teeth.
- Gear Ratio: The ratio of the number of teeth on the driven gear to the number of teeth on the driving gear.
- Gear Train: A series of gears that transmit power and motion between two or more rotating shafts.
- Gear Mesh: The point of contact between the teeth of two meshing gears.
- Load Capacity: The maximum load that a gear can transmit without failure.
How are Gears Made?
There are several ways to manufacture gears, including:
Hobbing: A process in which a gear blank is rotated against a cutter called a hob, which is shaped like the gear’s tooth profile.
Shaping: A process in which a gear blank is rotated against a cutter that is shaped like the gear’s tooth profile.
Milling: A process in which a gear blank is held stationary while a cutter is rotated against it to remove material and shape the gear’s tooth profile.
Grinding: A process in which a gear blank is held stationary while a grinding wheel is rotated against it to remove material and shape the gear’s tooth profile.
Broaching: A process in which a gear blank is pushed through a broach, which is a tool with cutting teeth that shape the gear’s tooth profile.
Gear cutting: A process in which a gear blank is rotated, and a cutter is moved along the gear’s circumference to shape the tooth profile.
In addition to these methods, gears can also be made by casting, forging, or 3D printing.