Sweep blasting, often referred to as brush-off abrasive blasting, is a vital process for those involved in galvanizing and fabricating, particularly when working with duplex coatings. This method balances the need for surface cleanliness with the preservation of protective zinc coatings, making it essential for preparing surfaces for additional layers of paint or powder coatings.
What is Sweep Blasting?
Sweep blasting is an abrasive blasting technique designed to be gentle enough to maintain the integrity of galvanized coatings while effectively cleaning and texturing surfaces. This process is particularly relevant for preparing hot-dip galvanized iron and steel products, as outlined in the ASTM D6386 and ASTM D7803 standards. These standards specify that sweep blasting can create a suitable surface profile for both paint and powder coating applications.
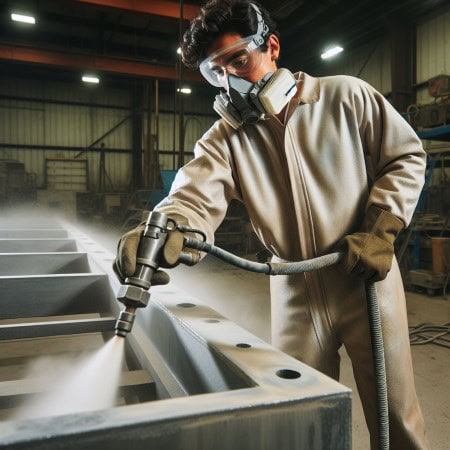
The Procedure for Sweep Blasting
The brush-off blast procedure aligns with the cleaning protocols established in ASTM D6386 and D7803. The primary aim is to deform the galvanized surface without removing excessive zinc. Operators must adhere to specific guidelines to achieve an acceptable surface profile of at least 0.75 mils while ensuring that no more than 1 mil of the zinc coating is stripped away. Here are key considerations for effective sweep blasting:
- Rapid Nozzle Movement: Quick movements help minimize the risk of zinc removal.
- Work Rate: Maintain a work rate of at least 1200 ft²/hr or higher.
- Blasting Medium Selection: Choose a suitable abrasive, such as:
- Aluminum/magnesium silicate (8 to 20 mils in size)
- Soft sands (MOHs hardness of five or less)
- Organic materials (like ground corn cobs or walnut shells)
- Corundum or limestone
- Blast Pressure: Adjust according to the abrasive medium, distance from the workpiece, and the geometric features of the item. Sometimes, even 20 to 40 psi may be excessive.
- Clean Compressed Air: Use uncontaminated air to avoid introducing impurities.
- Temperature Control: Ensure the substrate temperature is at least 5°F above the dew point.
- Post-Blasting: After the sweep blasting process, blow down the surface with clean compressed air, and apply the paint or powder coating promptly.
Standards and Specifications
The practice of sweep blasting is not only guided by galvanizing standards but also by the specifications set forth by the Society for Protective Coatings (SSPC). One key standard is SSPC-SP 16, which outlines the requirements for brush-off blast cleaning on both coated and uncoated galvanized steel, as well as other non-ferrous metals.
According to SSPC-SP 16, an adequately brush-off blasted surface must be free of visible contaminants such as oil, grease, dirt, dust, and corrosion products while achieving a minimum profile of 0.75 mils across the surface. This standard ensures that the cleanliness and surface profile are maintained, facilitating the successful application of protective coatings.
It’s important to note that while SSPC-SP 16 shares fundamental cleanliness requirements with SSPC-SP 7 (which applies to carbon steel substrates), the unique properties of non-ferrous metals like zinc necessitate specific attention during the blasting process.
Conclusion
In summary, sweep blasting is an essential technique for maintaining the effectiveness of galvanized coatings while preparing surfaces for additional protective layers. By adhering to established guidelines and standards, galvanizers and fabricators can ensure that their products not only meet industry requirements but also achieve optimal performance and longevity in their applications. Understanding and implementing proper sweep blasting procedures will ultimately enhance the quality and durability of finished products.