What does a good weld bead look like?
A good weld bead is one of the most important aspects of a successful welding application.
A good weld is essential for the safety and strength of a project, and the appearance of the weld bead can also play a role in its overall quality.
Whether you’re a professional welder or a hobbyist, understanding the fundamentals of what a good weld bead looks like can help you determine if your welding job has been done properly.
In this article, we’ll take a closer look at the characteristics that make up an ideal weld bead, including its shape and texture.
So, what does a good weld bead look like? Let’s explore the characteristics of a good quality weld bead, which welding process produces the best-looking welding bead, and how to spot a good weld bead.
What is a good weld?
A good weld is a joint between two or more pieces of metal that has been created using welding processes in such a way that it meets the desired strength, durability, and quality requirements of the application.
It should have consistent penetration, be free of defects like cracks or porosity, and have a smooth and even appearance.
Related reading: Welding Defects Types with pictures.

The weld should also blend seamlessly with the base metal and not create any weak points in the structure.
A good weld should also be visually acceptable, with a smooth, uniform, and continuous weld bead that blends seamlessly with the base metal.
A good weld is essential to ensure the structural integrity and safety of the welded components and to meet the design requirements of the application.
Characteristics of a good quality weld bead
A good quality weld bead should have the following characteristics:
- Consistent width and depth: The width and depth of the weld bead should be consistent throughout the entire weld, indicating that the heat and welding wire were applied evenly.
- Smooth appearance: The surface of the weld bead should be smooth and free of any bumps, craters, or irregularities. This indicates that the weld wire was melted and deposited evenly across the joint.
- No undercutting: Undercutting occurs when the edges of the base metal are melted away during the welding process, creating a groove or undercut in the weld. A good weld bead should be free of undercutting, which weakens the joint and can lead to cracking.
- Proper penetration: The weld bead should penetrate deeply into the base metal, creating a strong bond between the two pieces.
- No porosity: Porosity occurs when gas bubbles become trapped in the weld, creating holes that weaken the joint. A good quality weld bead should be free of porosity.
- Free from other Welding Defects: A good weld is free from welding defects such as cracks, slag inclusion, lack of penetration, overlap, end crater, smooth start-stop, etc.
Which welding process produces the best-looking welding bead?
The welding process that produces the best-looking welding bead depends on the type of metal being welded and the desired appearance.
Generally, TIG welding produces the best-looking weld bead because it produces a narrow and precise weld with minimal splatter.
However, MIG and Stick welding can also produce a good-looking weld bead with the proper technique and equipment.
How to spot a good weld bead?
To spot a good weld bead, look for the characteristics mentioned above. A good weld bead should be smooth, consistent, and free of defects like undercutting and porosity.
The weld should also blend seamlessly with the base metal and not create any weak points in the structure.
A good weld bead is essential for the safety and strength of a project, and its appearance can also play a role in its overall quality.

The quality of a weld determines how strong and reliable the joint will be, so it’s important to know how to identify a good weld. Spotting a good weld bead is not hard if you know what to look for.
A well-formed weld bead should have an even surface with no gaps or undercuts in the material. It should also have a consistent width along its length and the penetration should extend through both sides of the joint.
Additionally, there should be minimal spatter or slag on the finished product, as that could indicate poor welding technique.
In addition to these criteria, color can sometimes give an indication as to whether or not a good weld has been achieved; stainless steel typically produces silver beads while aluminum usually results in light gray beads.
By understanding the characteristics of a good quality weld bead, which welding process produces the best-looking welding bead, and how to spot a good weld bead, you can ensure that your welding projects are both strong and aesthetically pleasing.
How do I know if my welds are good?
Knowing whether your welds are good or not is important to ensure the safety and structural integrity of your project. Here are some ways to know if your welds are good:

- Visual Inspection: One way to check if your welds are good is by visually inspecting them. The weld bead should have a consistent width and depth, and the surface should be smooth and free of any bumps or irregularities. The weld should also blend seamlessly with the base metal and not create any weak points in the structure.
- Penetration Test: Another way to check the quality of your welds is by performing a penetration test. This involves cutting the welded joint in half and inspecting the depth of penetration. The weld should have deep penetration into the base metal, indicating a strong bond between the two pieces.
- Destructive Testing: In some cases, destructive testing may be necessary to determine the quality of the weld. This involves subjecting the welded joint to extreme stress or pressure to see if it holds up. If the joint fails or breaks, it indicates a weak or faulty weld.
- Non-Destructive Testing: Non-destructive testing methods such as ultrasonic testing or X-ray inspection can be used to detect any internal defects or inconsistencies in the weld.
- Consult a Professional: If you are unsure about the quality of your welds, it is always best to consult with a professional welder or inspector. They can provide expert advice and guidance on how to improve the quality of your welds and ensure the safety and integrity of your project.
In conclusion, by performing visual inspections, penetration tests, destructive and non-destructive testing, and consulting with a professional welder or inspector, you can ensure that your welds are of good quality and meet the necessary safety standards.
What are the characteristics of a bad weld bead?
A bad weld bead can compromise the strength and safety of a project. Here are some characteristics of bad weld beads:
- Inconsistency in width and depth: A bad weld bead may have inconsistencies in the width and depth of the bead, indicating that the heat and welding wire were not applied evenly.

- Craters and bumps: The surface of a bad weld bead may have craters or bumps, indicating that the weld wire was not melted and deposited evenly across the joint.
- Undercutting: Undercutting occurs when the edges of the base metal are melted away during the welding process, creating a groove or undercut in the weld. A bad weld bead may have undercutting, which weakens the joint and can lead to cracking.
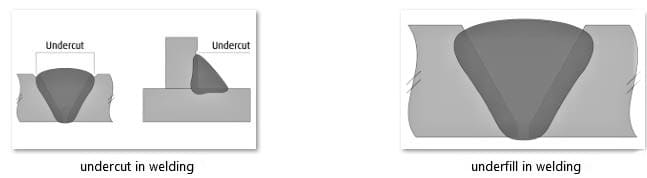
- Porosity: Porosity occurs when gas bubbles become trapped in the weld, creating holes that weaken the joint. A bad weld bead may have porosity, indicating that the weld was not properly shielded from the surrounding air.

- Cold lap: Cold lap occurs when the weld metal does not fuse with the base metal, resulting in a weak joint. A bad weld bead may have cold lap, indicating that the weld was not properly heated or applied.
- Overlap: Overlap occurs when excess weld metal is deposited on the joint, resulting in a weak joint. A bad weld bead may have overlap, indicating that the welder applied too much heat or welding wire to the joint.

In summary, a bad weld bead can have inconsistencies in width and depth, craters and bumps, undercutting, porosity, cold lap, and overlap.
These characteristics can weaken the joint and compromise the safety and structural integrity of the project. It is important to take the time to ensure that welds are done properly to avoid these issues.
References: