What Is Steel Fabrication?
Steel fabrication is the process of creating a steel product from scratch. This can include anything from large structural beams to small metal parts. The fabrication process begins with the selection of the right type of steel for the job. The steel is then cut to size and shape, before being welded together. Finally, it is finished with a protective coating to prevent corrosion.
So, Steel fabrication is the process of turning a piece of steel into a final product. The first step is to get the raw material. Steel comes in different shapes and sizes, so the fabricator needs to choose the right piece for the job.
Then they start cutting and welding it into the desired shape. Finally, they do any finishing work that’s needed. This can include painting, polishing, or adding logos or other decorations.
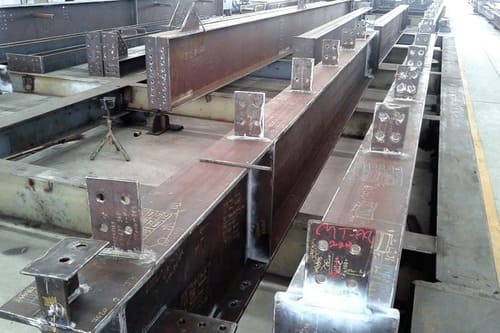
What is Fabrication Definition?
When most people think of fabrication, they think of the metalworking process of shaping and bending materials like steel and aluminum. However, fabrication is actually a very general term that can be used to describe any manufacturing process.
In fact, the word “fabrication” comes from the Latin word fabricare, which means “to make.” So essentially, fabrication is any process by which something is made. This could include processes like welding, machining, and casting. It could also include more traditional methods like sewing and weaving.
Steps for Steel Metal Fabrication Process
Steel metal fabrication is a process that takes steel and converts it into useful objects like structure (Bridge, building), gates, fences, cars, and more. There are many steps in the process, but some of the most important ones are cutting the steel to size, bending it to the desired shape, welding it together, and then painting or powder coating it.
The Basic Steps for Steel Metal Fabrications are marking, Cutting, Machining, Fitment, Welding, blasting & Painting or Coating. A brief overview of these Steps are:
1. Marking:
When fabricating parts, it is important that all dimensions are clearly marked and understood. In order to ensure accuracy, it is also necessary to use the correct drawing. Marking of plates are carried out for manual cutting while CNC machines relies of Auto Cad drawings for cutting.
2. Cutting:
The next step in the Steel Fabrication process is to cut the steel to size. This can be done with a variety of machines, including lasers, plasma cutters, and water jets. Once the steel is cut to size, it is then bent to the desired shape. This can be done manually or with machines like press brakes and rollers.
3. Bending/ Forming/ Rolling
In metalworking or Steel Fabrication, plate bending, forming or Rolling is the process of shaping a sheet of metal by localized deformations. The sheet is placed between two rollers, called bending rolls, and then compressed. This causes the sheet to deform into a curved shape. Plate bending can be used to create simple bends or more complex shapes.
4. Machining:
Machining is a process that uses controlled cuts to shape or finish a workpiece. The most common type of machining is milling, which involves using a rotating cutter to remove material from a workpiece. Other types of machining include turning, drilling, and grinding.
Machining is often used to fabricate parts for machinery and other devices. By using a variety of cutting tools, machinists can create parts with precise dimensions and smooth surfaces. Machining can also be used to modify existing parts, such as by drilling holes or adding threads.
5. Parts Fitment & Tacking:
Fitment is one of the most important aspects of fabrication. A good fit ensures that a part will function as intended and look good while doing it. There are a few tricks to achieving a good fit, but the most important part is starting with accurate measurements.
Fabricators use a variety of techniques to achieve a good fit, but the most common is tacking. Tacks are temporary welds that hold parts in place while you adjust them to get a good fit. Once everything is aligned, the tacks are welded permanently. This process allows fabricators to make small adjustments until everything is perfect.
6. Welding:
After it is bent to shape, the welders come in and weld it together. They use a variety of techniques depending on what type of weld they are doing. Welding is the process of joining two pieces of metal together by heating the metal to a point where it melts and then using a filler material to bond the two pieces together. The most common welding process is called Stick Welding (SMAW), gas tungsten arc welding, or GTAW, & FCAW, which uses an electric arc to heat the metal. There are many different types of welding processes, each with its own advantages and disadvantages.
Welding is used in many industries for fabricating parts from steel. It is a very versatile process and can be used for both small and large parts. Welding can be used to make simple joints, or it can be used to fabricate complex shapes. Many times, welding is the only way to fabricate certain parts from steel.
What Does Fabricate Means?
Fabricating is the process of creating a part or component from raw materials. In welding, fabricating means to create a component by welding together smaller pieces. This may involve creating a custom shape or size, and can be done using a variety of welding methods. Fabricated parts are often stronger and more durable than those that are manufactured using traditional methods.

What is Steel?
Steel is a type of alloy made from iron and carbon. The carbon content can range from 0.02% to 2.14% by weight, depending on the grade of steel. Adding carbon to iron makes it harder and stronger than pure iron, which is why steel is so commonly used in construction, engineering, and manufacturing. There are many different grades and types of steel, each with its own unique properties. Some common types of steel include mild steel, stainless steel, tool steel, and cast iron.
The other main alloying elements are usually chromium, manganese, nickel, and copper. Steel has a variety of uses, the most common of which are in construction and manufacturing. It is strong and durable, making it ideal for these applications. Steel also has good heat and corrosion resistance, making it a popular choice for many industrial applications. It is relatively affordable compared to other metals such as aluminum or brass.
What’s the Basic Raw Materials required for Steel Metal Fabrication?
There are many different types of materials that are used in the fabrication of metal products. The most basic raw materials are metals such as iron and aluminum. Alloys are created by combining metals with other elements, such as copper, nickel, and zinc. In addition to alloys, a variety of other materials can be used in metal fabrication, including plastics, ceramics, and glass welding.
The type of material that is used depends on the product that is being manufactured. For example, products that require high strength and durability, such as automobiles or aircraft parts, are usually made from alloys of various metals. Products that need to be lightweight or corrosion-resistant might be made from plastics or other synthetic materials.
No matter what material is used, the process of fabricating metal products always begins with cutting the metal into the desired shape.
Who is a Fabricator?
A fabricator is a skilled tradesman who manufactures objects from steel, structural members or other materials. Fabricators work in a variety of industries, including automotive, aerospace, and construction. They may be employed by companies that produce finished products or by companies that provide services to others in the manufacturing process.
Fabricators typically have a high school diploma or equivalent and receive on-the-job training. Some fabricators may become certified in specific welding or machining processes.
The work of a fabricator is highly skilled and requires precision and attention to detail. Fabricators must be able to read blueprints and specifications, operate complex machinery, and make precise measurements. They must also be able to work safely in a factory environment.
Fabricated Steel Structure Overview
Steel is a widely used material in construction, and it is often fabricated into different shapes to create the desired structure. Steel can be easily molded into different shapes and sizes, making it a versatile material for many applications. When used for fabrication, steel can be cut and welded together to create a variety of structures.
Steel is a composite material consisting of iron and carbon. The carbon content can range from 0.002% to 2.14% by weight, depending on the grade of steel. The higher the carbon content, the harder and stronger the steel becomes. There are many different grades of steel, each with its own unique set of properties that make it suitable for a particular application.
Steel is most commonly used in construction because it is strong and durable. It can be used in both structural and non-structural applications. Steel is also relatively lightweight compared to other materials like concrete or masonry, which makes it ideal for use in buildings and other structures.
The process of fabricating a steel structure begins with the fabrication of the steel members. The members are then assembled into a frame or skeleton that will become the foundation of the structure.
Stainless Steel Fabrication overview
Stainless steel fabrication is a process that takes a sheet of stainless steel and cuts, bends, and welds it into the desired shape. The most common type of stainless steel is 304, which is a versatile and affordable option for many applications. Stainless steel fabrication can be used to create a wide variety of products, including countertops, sinks, trim, and more.
There are many different methods for fabricating stainless steel, so it’s important to choose a fabricator who has experience with your specific type of steel. The fabricator will work with you to create a design that meets your needs and fits within your budget. They will also be able to recommend the best materials and finishes for your project.
If you’re looking for quality stainless steel fabrication services, contact a local fabricator today.
Similar Posts: