Water Jet Cutting
Water jet cutting is a modern cutting technology that uses high-pressure water streams to cut through various materials, including metal, stone, glass, and composites.
This cutting method is known for its precision and versatility, as it can produce intricate shapes and designs with minimal waste.
Water jet cutting has become increasingly popular in manufacturing, art, and other industries due to its ability to cut through materials that are difficult or impossible to cut using traditional cutting methods.
In this blog post, we will explore the basics of water jet cutting, how it works, its advantages and disadvantages, and its various applications.
What is Water Jet Cutting?
Water jet cutting is a versatile method of cutting a range of materials, both metallic and non-metallic, by using a powerful jet of water.
This jet is created by pushing water at high pressures, between 30 ksi and 60 ksi, through a small orifice typically made of sapphire measuring 0.004 inches to 0.024 inches (0.1 mm to 0.6 mm) in diameter.
While it is not a thermal cutting process, water jet cutting does produce a kerf through concentrated water jet erosion.

Unlike traditional machine tool cutting methods, water jet cutting is a process that uses a high-pressure jet of water to cut through materials.
This method involves forcing water through a small orifice, typically made of sapphire, at pressures between 30 ksi and 60 ksi, resulting in a powerful water jet that can cut through a variety of materials.
Although it is not a thermal cutting process, water jet cutting produces a kerf through concentrated water jet erosion, making it somewhat similar to thermal cutting methods.
Water jet cutting is a non-thermal cutting process that uses a high-pressure jet of water to cut through a range of materials, including both metallic and non-metallic materials.
This powerful jet is created by forcing water through a small orifice made of sapphire, with diameters ranging from 0.004 inches to 0.024 inches (0.1 mm to 0.6 mm), at pressures between 30 ksi and 60 ksi.
While water jet cutting does not employ a machine tool cutting device, it is similar to thermal cutting techniques in that it produces a kerf through concentrated water jet erosion.
How WaterJet Cutting Works?
Waterjet cutting is a process of cutting a wide range of materials using a high-pressure stream of water. The process involves the use of specialized machinery, which creates a jet of water that is pressurized up to 60,000 PSI (pounds per square inch) or higher. The waterjet stream is then directed towards the material to be cut, where it erodes the material, creating a precise cut.
The waterjet stream can be mixed with abrasive materials such as garnet, aluminum oxide, or diamond particles, to increase the cutting power of the stream. This is known as abrasive waterjet cutting and is used for materials such as metals, ceramics, stone, and composites.
The process involves several components, including a high-pressure pump, water jet nozzle, abrasive mixing chamber, cutting table, and computer-controlled software. The high-pressure pump creates the pressure necessary to create the waterjet stream. The waterjet nozzle is where the stream is created, and the abrasive mixing chamber is where abrasive materials are added to the stream.
The cutting table is where the material to be cut is placed, and the computer-controlled software directs the waterjet stream to create the desired shape or pattern. The cutting speed, pressure, and direction of the waterjet stream can all be controlled by the software.
Advantages of Water jet Cutting
Water jet cutting offers several advantages over traditional cutting methods, including:
- Versatility: Water jet cutting can cut through a wide range of materials, including metals, stone, glass, plastics, and composites. This makes it a versatile cutting method for a variety of applications.
- Precision: The high-velocity water jet can be controlled very precisely to cut intricate shapes and designs, with a high degree of accuracy and repeatability.
- No Heat-Affected Zone: Unlike thermal cutting methods, water jet cutting does not generate heat, which can cause distortion, warping, or other damage to the material being cut. This means that water jet cutting can be used on materials that are sensitive to high temperatures.
- Minimal Material Waste: Water jet cutting produces a narrow kerf, which means that less material is wasted compared to other cutting methods. This can help to reduce costs and improve efficiency.
- Environmentally Friendly: Water jet cutting is a clean, environmentally friendly cutting method, as it does not generate harmful fumes, dust, or other pollutants. Additionally, the water used in the cutting process can be recycled and reused, further reducing waste.
Disadvantages of Water jet Cutting
While water jet cutting has many advantages, there are also some disadvantages to consider. Here are a few:
- Cost: Water jet cutting machines are generally more expensive than other cutting tools, and the operating costs can be high as well due to the cost of the equipment, the need for specialized training, and maintenance costs.
- Limited thickness: While water jet cutting can cut through a wide range of materials, the thickness that can be cut is limited compared to other cutting methods. Thicker materials may require multiple passes, which can be time-consuming and costly.
- Environmental impact: Water jet cutting produces a lot of waste water, which can contain abrasive particles and other materials. This can make it more difficult to dispose of the water safely and can lead to environmental concerns.
- Noise and vibration: Water jet cutting machines can produce a lot of noise and vibration, which can be a concern in some settings. This can be mitigated by using soundproofing materials or locating the machine in a separate area.
- Slow cutting speed: While water jet cutting is very precise, the cutting speed is generally slower than other cutting methods. This can be a concern in some applications where time is of the essence.
Water Jet Cutting vs Plasma Cutting
Criteria | Water Jet Cutting | Plasma Cutting |
---|---|---|
Cutting Speed | Slow to Moderate | Moderate to Fast |
Material Thickness | Up to 200 mm | Up to 150 mm |
Cutting Accuracy | High | Moderate |
Heat Affected Zone | Minimal to None | Significant |
Material Limitations | Almost None | Conductive Materials Only |
Edge Quality | Smooth | Rough |
Environmental Impact | Minimal | Air Pollution |
Noise Level | Low | High |
Operating Cost | High | Low to Moderate |
Initial Investment | High | Low to Moderate |
Note: The comparison is based on general observations and may vary depending on the specific application and machine used.
Water Jet Cutting vs Laser Cutting
Features | Water Jet Cutting | Laser Cutting |
---|---|---|
Cost | High | Medium to High |
Speed | Slow | Fast |
Material Range | Can cut virtually any material, including metals and nonmetals, thick or thin | Primarily limited to metal and some nonmetal materials |
Precision | Excellent | Very good to Excellent |
Edge Quality | Good | Excellent |
Heat Affected Zone | Minimal | Significant |
Maintenance | High | Low |
Environmental Impact | Low | Medium to High |
Safety | High | Medium |
Water jet cutting and laser cutting are both popular methods for cutting a wide range of materials.
However, they have some notable differences. Water jet cutting can cut virtually any material, while laser cutting is primarily limited to metal and some nonmetal materials.
Water jet cutting is slower but offers excellent precision, while laser cutting is faster but has slightly less precision.
Water jet cutting produces minimal heat affected zones and has low environmental impact, but requires high maintenance.
Laser cutting has excellent edge quality but produces a significant heat affected zone and has medium to high environmental impact.
Water Jet Cutting vs Gas Cutting
Water Jet Cutting | Gas Cutting |
---|---|
Can cut a wide variety of materials, including metals and non-metals | Limited to cutting ferrous metals |
No heat-affected zone (HAZ), resulting in minimal distortion or warping | Creates a HAZ, leading to distortion or warping |
High precision cutting with tight tolerances | Limited precision cutting |
Does not produce hazardous fumes or waste materials | Produces hazardous fumes and waste materials |
Requires high-pressure water and abrasive, which can be costly | Gas fuel is generally cheaper than water and abrasive |
Slower cutting speed compared to gas cutting | Faster cutting speed compared to water jet cutting |
Water Jet Cutting Speeds for Various Materials
Water jet cutting is a versatile cutting method that can be used on a variety of materials.
The cutting speed for water jet cutting can vary depending on the material being cut.
Here are the approximate cutting speeds for some common materials:
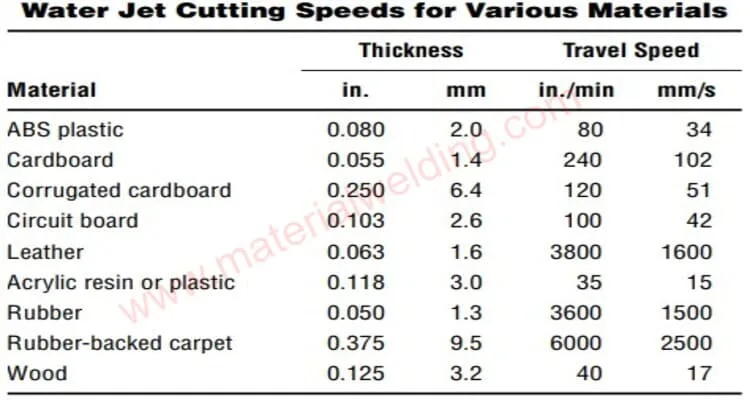