Why do we need to calculate Weld Deposition Rate?
The costs of any manufacturing process such as welding, machining, or cutting, etc. can be accurately calculated using the right approach and considering the essential related expenses & overheads.
For welding cost calculation, one of the important factors is the Deposition Rate or rate of weld deposit per hour. Other factors for welding cost calculations are:
1. Labor
2. Welding consumables- Electrode, filler wire, flux, etc.
3. Overhead expenses
Before bidding for a project, cost analysis is the prerequisite to reaching a competitive selling price to win a project related to welding.
The method given here is related to the calculation of the welding deposit rate only which is one of the factors related to finding the welding cost. Here, the most common welding deposition rate calculation methods are given.
Many times we as a Welding Engineers find ourselves in a situation looking for answers:
- How many Kilogram of welding rods I can deposit/hr?
- What is the wire deposition rate at different welding amperage settings?
- What will be the cost of welding wire for a project?
- What will be the cost of Welding jobs for a particular client?
Do you Know What is Deposition rate in Welding?
Straightforward answer: How much weld metal is deposited by a welding process in a unit time. Unit team here is kilogram(or pound) per hour, hence the unit of deposition rate in welding is kilogram/hour (kg/hr) or pound per hour (lb/hr).
The need for higher weld deposition rate or lower deposition rate depend on the job requirements.
- When welding thin metal, open root run welding, exotic material welding, we need low deposition rate.
- When welding thick joints, fillet welds and piping jobs, it is usually desired to have high welding deposition rate.
Deposition rate (DR) vs. melt off rate (MOR)
Before you use this calculation, it’s important to understand the difference between weld deposition rate & MOR, as both are different terms.
Deposition rate (DR) in welding refers to the speed with which a welding rod/wire is melted and deposited as a weld.
The Unit of DR is pounds per hour or kg/hr. Whereas, the Melt-off rate (MOR) is the total weight of the welding consumable fused in a unit of time. Melt-off rate is also given in terms of lb/hr (pounds per hour) or kg/ hr.
Welding Deposition Rate Formula with sample Calculation
Welding Deposition Rate Formula = X x (D²) (FR)(Y) in pounds/ hour
- d = Dia. of welding rod
- FR = Wire-feed rate (inches/minute) in case of GMAW/ SAW/FCAW- consider electrode burn-off rate for stick welding or SMAW.
- Y =Electrode Efficiency,
- X =13.1 (Constant for Steel based on steel density. This constant is applicable for carbon steel and stainless steel welding filler wires. For Aluminum the value of X is 4.32).
Example calculation for GMAW (MIG/ MAG & FCAW Process):
Calculate the weld deposit rate for carbon steel pipe welding using GMAW with a wire-speed rate of 70 ipm (inch per minute) using an electrode diameter of 0.035 inches.
Calculation= 13.1 x 0.0352 x 70 x0.98 = 1.1 pounds/ hour.
The above calculation examples suits for welding applications where you can read the wire feed speed on the welding machine. Examples: MIG, FCAW, Automated TIG such as orbital TIG, and SAW).
Example calculation for Stick Welding (SMAW)
Calculate the welding deposit rate for Fillet welding welded with Stick welding using 1/8 inches diameter welding rod .
Calculation= 13.1 x 1/82 x 10 x0.8 = 1.64 pounds/ hour.
Where: 13.1 constant for Stainless steel, 1/8 is electrode diameter, 10 is burn off rate and 0.8 is efficiency for stick welding.
Burn-off rate in stick welding (SMAW) need to be verified by checking what rod length is consumed in a minute. It depends on different factors and hence to be checked for exact value.
Electrode Efficiency (Y) in Welding
Electrode efficiency (Y or also denoted by EE) is the Percentage of Melt-off rate (MOR) contributing to Deposition efficiency.
EE for solid fillers can basically depend on the metal transfer mode in welding. As each metal transfer mode has varied characteristics that define how molten metal is transferred to the weld pool & associated losses during transfer such as spatters or metal vaporization.
Listed below are the electrode deposit efficiencies for different metal transfer modes in GMAW:
- Short-circuit metal transfer Mode: 89-94%
- Surface metal transfer Tension Mode: 97%
- Spray metal transfer Mode: 97%
- Globular metal transfer Mode: 87 – 91%
- Pulsed metal transfer mode: 95- 98%
Electrode Efficiency (Y) for Stick, TIG & SAW Welding
- Stick Welding (SMAW): 80%
- TIG Welding: 95%
- FCAW Welding: 92%
- SAW Welding: 95%
What is percentage of deposition efficiency in fcaw process?
The percentage of deposition efficiency in FCAW process is 92%. This efficiency is approximate and there can be some variations based on the welding amperage, welding position and wire-cut out losses.
General Weld Deposit Rate in Different Welding Processes
The below table gives indicative weld deposit rates for SMAW, GMAW, FCAW, and SAW.
As we know, various factors (current, electrode diameters, single or double electrode, welding position, metal transfer mode, etc.) influence the weld deposit rates, values stated here are for indicative purposes only.
Deposit rate in SMAW Process
E6010 x 3.2 mm @ 115 A … … … 1.25 kg/hr (2.82 lb/hr)
E6012 x 3.2 mm @ 115 A … … … 1.05 kg/hr (2.22 lb/hr)
E7014 x 4.0 mm @ 180 A … … … 1.82 kg/hr (4.0 lb/hr)
E7018 x 4.0 mm @ 180 A … … … 1.82 kg/hr (4.0 lb/hr)
E7024 x 3.2 mm @ 140 A … … … 1.41 kg/hr (3.1 lb/hr)
E7024 x 4.0 mm @ 210 A … … … 2.09 kg/hr (4.6 lb/hr)
Deposit rate in FCAW Process
E711T x 1.6 mm @ 275 A … … … 5.00 kg/hr (11 lb/hr)
E711T x 2.4 mm @ 400 A … … … 5.46 kg/hr (12 lb/hr)
Deposit rate in GMAW Process
ER70S-6 x 0.9 mm @ 175 A … … … 2.05 kg/hr (4.5 lb/hr)
ER70S-6 x 1.2 mm @ 175 A … … … 1.68 kg/hr (3.7 lb/hr)
ER70S-6 x 1.2 mm @ 225 A … … … 2.36 kg/hr (5.2 lb/hr)
ER70S-6 x 1.2 mm @ 270 A … … … 3.73 kg/hr (8.2 lb/hr)
Deposition Rate Welding for Different Processes
In welding, deposition rate is influenced by many factors such as rod diameter, welding amperage, travel speed, welding process atomization level and welding process.
In below table, you can find indicative deposition rate in welding for common welding processes. This welding deposition rate (kg/hr) can be change from minimum to maximum depending on above factors.
– | DR in kg/hr Minimum | DR in kg/hr Minimum |
---|---|---|
Stick Welding | 0.3 kg/hr | 6 kg/hr |
MIG Welding | 0.5 kg/hr | 14 kg/hr |
Flux Core Welding | 1.1 kg/hr | 14.5 kg/hr |
Submerged Arc Welding | 3 kg/hr | 16 kg/hr |
Which Welding Process offer highest welding deposition rate?
Welding deposition rate is directly proportional to the electrode feed rate (welding amperage) and travel speed.
Welding process such as TIG welding, where rod feed rate is very low results in lowest weld deposition rate. Submerged arc welding, where a higher rod diameter and high welding amperage used, result in highest weld deposition rate.
Stick welding deposition rate is higher than TIG welding but lesser than MIG, FCAW and SAW Welding.
How Welder can increase the Welding Deposition Rate?
If Welder has option to increase the welding deposition rate, these are the best choice they must make:
- Welding in flat position.
- Use higher diameter welding rod.
- Use higher welding amperage is permitted.
- Look for automated welding process option such as orbital TIG.
- Welding using MIG, FCAW instead of Stick Welding.
What are the disadvantages of Higher Deposition rate?
A high welding deposition rate is not always beneficial and there can be following disadvantages of higher weld deposition:
- It can create high heat input and thus distortion in parts.
- It can result in poor welding quality.
- High welding deposition can cause high weld dilution when welding dissimilar welding of weld cladding.
- High weld deposition, higher welding fumes, heat and spatters.
Weld Deposition Rate Chart
Weld deposition rate chart for stick welding (SMAW) process is given in the below table. This chart provide estimate for weld deposited rate by entering the value of welding amperage.
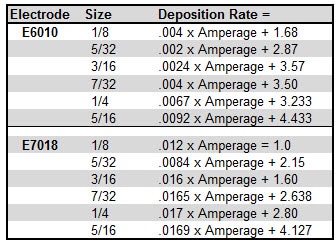
excellent post.
Valuable information. thanks