A rebar size chart is an essential tool for any builder, contractor or engineer in the construction industry. Knowing the correct specifications for rebar is paramount to building a reliable and durable structure.
Rebar comes in a variety of sizes and can be used in both vertical and horizontal applications. To ensure accuracy when using rebar, it’s important to know the exact dimensions that are required for your project.
A rebar size chart provides easy-to-understand guidelines on sizing and spacing so you can get exactly what you need for your project.
The chart typically lists the Rebar Size, weight per unit length (lb/ft or kg/m), area of steel per unit length, diameter, area as well as other important information about each type of rebar available.
Rebar Size and Rebar Weight Chart
The industry standard metric for measuring rebar is kilograms per meter (kg/m). This measurement indicates how much weight each bar can bear over its entire length before breaking or buckling.
The ASTM A955/ A955M is a standard that provides a rebar size chart for metric and imperial sizes. It is used by engineers to more accurately determine the diameter, area, and weight of reinforcing bars.
Imperial Bar Size | Weight (lb/ft) | Weight (kg/m) | Nominal Diameter (in) | Nominal Diameter (mm) | Nominal Area (in2) | Nominal Area (mm2) |
---|---|---|---|---|---|---|
3 | 0.376 | 0.561 | 0.375 | 9.525 | 0.110 | 71 |
4 | 0.688 | 0.996 | 0.500 | 12.700 | 0.200 | 129 |
5 | 1.043 | 1.556 | 0.625 | 15.875 | 0.310 | 200 |
6 | 1.502 | 2.240 | 0.750 | 19.050 | 0.440 | 284 |
7 | 2.044 | 3.049 | 0.875 | 22.225 | 0.600 | 387 |
8 | 2.670 | 3.982 | 1.000 | 25.400 | 0.790 | 509 |
9 | 3.400 | 5.071 | 1.128 | 28.650 | 1.000 | 645 |
10 | 4.303 | 6.418 | 1.270 | 32.260 | 1.270 | 819 |
11 | 5.313 | 7.924 | 1.140 | 35.810 | 1.560 | 1006 |
14 | 7.650 | 11.410 | 1.693 | 43.000 | 2.250 | 1452 |
18 | 13.600 | 20.284 | 2.257 | 57.330 | 4.000 | 2581 |
How to Read Rebar Marking?
Rebar, also known as reinforcing bar, is a vital component in reinforced concrete and masonry structures.
Read more: Rebar Welding Guide.
Properly deciphering rebar marking can ensure that the structure is built to code and to its intended specifications.

- The 1st letter is for the rebar manufacturing symbol or logo.
- 2nd letter is for the Rebar Size. E.g., #3, #4, or so on. The below rebar example size is #11.
- 3rd letter on the rebar is for the type of Rebar materials. E.g., S for carbon steel, W for Low alloy steel, SS for stainless steel, R for rail steel, A for Axle steel, etc.
- 4th letter is for the grade mark that corresponds to the minimum yield strength of the rebar.
Here are some simple tips on how to read rebar marking so that you can be sure your job meets all safety standards.
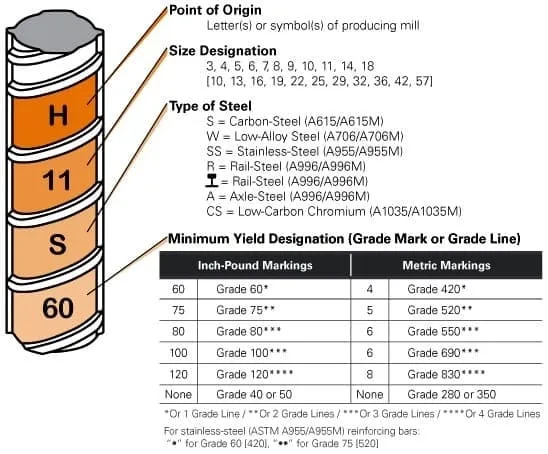
Types of Rebars
Rebar is short for “reinforcing bar” and is used to reinforce concrete in order to improve its tensile strength. Rebar comes in many different types, each designed for specific applications and environments.
- Mild Steel and Carbon Steel Rebar,
- Deformed Steel Rebar: TMT & High strength rebars,
- Low Alloy steel Rebar,
- Stainless steel Rebar,
- Galvanized steel Rebar,
- Glass fiber reinforced polymer (GFRP) Rebar,
- Epoxy-coated rebar,
- Welded wire mesh Rebar, and
- High-tensile steel Rebar.
1. Mild Steel/ Carbon Steel Rebar
Mild steel carbon steel rebar is a type of reinforced concrete material commonly used in the construction industry for its strength and durability. Rebar, short for reinforcing bar, is composed of mild steel which contains a small amount of carbon.
The addition of carbon gives this type of steel its superior strength and makes it ideal for use in structural applications such as bridges, buildings and other large structures where stability is critical.
Mild steel carbon steel rebar has the ability to be bent, twisted or straightened without breaking while providing high levels of corrosion resistance thanks to the small amount of carbon present in the alloy composition.
2. Deformed Steel Rebar: TMT & High strength rebars
Deformed steel rebar, often referred to as Saria or TMT bars, is an essential component in the construction industry.
These bars are created by subjecting mild steel to a thermal and mechanical treatment process which strengthens them significantly more than plain carbon steels.
This additional strength makes them ideal for applications requiring tensile strength and added stability such as bridge and highway construction, building foundations and retaining walls.
There are two types of deformed steel rebar – TMT (Thermo-Mechanically Treated) bars and high strength rebars. TMT bars are produced through a combination of hot rolling, heat treatment and cooling procedures that result in great ductility with increased bond strength between the concrete and bar.
High-strength rebars feature greater tensile yield strengths compared to conventional grade reinforcement materials making them suitable for use in seismic or other specialist applications including offshore structures.
3. Stainless steel Rebar
Stainless steel rebar, as per ASTM A955 and BS 6744 standards is a highly durable and versatile material that can withstand extreme environmental conditions.
It is known for its superior corrosion resistance and anti-rust properties, making it ideal for use in industrial environments exposed to harsh weather conditions such as saltwater or high humidity. The grade of stainless steel used for manufacturing this rebar meets the highest standards in terms of strength, durability, and other mechanical properties which means that it can be safely used in any environment where there may be exposed to strong chemicals or other corrosive elements.
Moreover, stainless steel rebar manufactured according to ASTM A955 and BS 6744 standards has greater tensile strength than most other materials due to its ability to maintain good physical properties even when exposed to various temperatures and climate conditions.
4. Galvanized steel Rebar
The process of galvanizing involves coating the steel rebar with a layer of zinc oxide which helps protect it from rust and corrosion.
This protective layer is extremely durable, making it ideal for outdoor applications where exposure to the elements can cause significant damage over time.
The galvanization process ensures that each bar or mesh offers superior protection against rust, making it suitable for harsh environmental conditions such as coastal regions or areas where there are high levels of humidity.
5. Glass fiber reinforced polymer (GFRP) Rebar
Glass Fiber Reinforced Polymer (GFRP) Rebar is a new and revolutionary construction material that is revolutionizing the way structures are constructed. It is strong, durable, and corrosion-resistant.
GFRP rebar has been proven to outperform traditional steel in terms of strength while also being lighter and easier to install. it has an impressive strength-to-weight ratio which makes installation easier than ever before; this also reduces the need for heavy equipment during construction.
The composite properties of GFRP Rebar provide enhanced durability compared to regular steel rebar. In addition, the GFRP bar does not corrode or deteriorate quickly like conventional bars do when exposed to harsh environmental conditions such as high temperatures or chemicals – an ideal choice for infrastructure projects located near salt water or other aggressive elements.
GFRP rebar can be made in longer lengths, allowing fewer joints and less labor compared to conventional reinforcing bars. This ensures greater structural integrity and less risk of failure due to inadequate connection points.
Finally, GFRP rebar is non-conductive, providing increased safety when working with large amounts of electricity or near utility lines.
6. Epoxy-coated rebar
This type of reinforcement steel is coated with an epoxy resin that helps protect the steel from rust and other forms of deterioration. The coating adds additional tensile strength to the rebar and provides a longer lifespan than traditional uncoated bars.
Additionally, it is more aesthetically pleasing than plain steel bars, making it ideal for structural elements exposed to public view.
Due to its increased longevity compared to uncoated rebar, epoxy-coated rebar can be used in areas with high moisture or acidity levels such as coastal locations or in swimming pools. It also offers superior protection against chemical attacks when used near soil contaminated with industrial pollutants or hazardous materials like heavy metals.
7. Welded wire mesh Rebar
Welded wire mesh rebar is a type of reinforcement that provides additional strength and stability to concrete structures. It is made from steel wires that are welded together in a grid pattern, creating a strong material with superior tensile strength.
The widespread use of welded wire mesh rebar makes it an attractive option for many construction projects due to its cost-effectiveness, time saved during installation and the enhanced stability provided by its uniform structure.
It also has excellent fire-rating properties and can be used in seismic zones due to its high ductility and flexibility. Additionally, they are easy to transport since they come pre-welded and require no extra cutting at the job site.
Rebar Diameters and Sizes
Rebar is available in a variety of sizes, ranging from #3 to #18 diameters. A number 3 rebar has an approximate diameter of 0.375 inches while the largest size (#18) measures 2.23 inches in diameter.

The type of project and the load-bearing capacity required will determine the correct size for each job.