Welding Rod Sizes
Welding rods, also known as filler metals or welding electrodes, are used to produce weld metal and fill the welding joint.
The size of the welding rod is determined by its diameter, and the type of welding process and the thickness of the metal being welded along with other factors covered in this article.
What are the Common sizes of welding rods?
When choosing a welding rod, it is important to select the appropriate size for the type of welding you will be performing and the thickness of the metal you will be welding.
A smaller diameter rod is good for sheet metal but will give low weld deposit volume on other hand side, bigger diameter rods produce high amount of weld deposit but also high welding heat and can’t be used for thin sheets welding. However, they are best for welding thick materials.

The most common sizes of Stick welding rods are:
- 3/32 inch (2.4 mm): This size of rod is commonly used for welding light gauge metal and for tack welding.
- 1/8 inch (3.2 mm): This size of rod is commonly used for welding medium gauge metal and for tack welding.
- 5/32 inch (4 mm): This size of rod is commonly used for welding heavy gauge metal and for tack welding.
- 3/16 inch (5 mm): This size of rod is commonly used for welding heavy gauge metal and for tack welding.
Below are the standard welding electrode sizes and lengths as specified in AWS A5.1 specification.pdf.

Welding Rod Sizes with Amperage Chart
You can use below welding rod sizes chart to choose the welding amperage for different diameters of welding rods used for carbon steel welding. The table is published in AWS A5.1 specification.

What are the Common sizes of TIG welding rods?
TIG welding, or Tungsten Inert Gas welding, is a type of welding that uses a non-consumable tungsten electrode to produce the weld.
The common sizes of TIG welding rods include 1/16-inch, 3/32-inch, 5/32 inch, and 1/8 inch.
The size of the TIG welding rod, also known as the filler metal, is determined by the thickness of the material being welded and the desired strength of the weld.
- 1/16 inch TIG welding rod is typically used for welding thin materials or for making small, precise welds.
- 3/32 inch TIG welding rod is commonly used for welding thin to medium thickness materials and for making strong, precise welds.
- 5/32 inch TIG welding rod is commonly used for welding medium thickness materials and for making strong, precise welds.
- 1/8 inch TIG welding rod is typically used for welding thick materials or for making strong, heavy-duty welds.
How to choose the correct stick welding rod size?
Choosing the correct stick welding rod size is important to ensure a strong and effective weld. Here are a few key factors to consider when selecting the appropriate rod size:
- Welding process: Different welding processes will require different rod sizes. For example, in the Shielded Metal Arc Welding (SMAW) process, the rod size is determined by the thickness of the metal being welded.
- Metal thickness: The thickness of the metal being welded is a crucial factor in determining the appropriate rod size. Generally, thicker metal will require a larger rod, while thinner metal will require a smaller rod.
- Welding position: The position of the weld (horizontal, vertical, overhead) will also affect the appropriate rod size. For example, welding in the vertical or overhead position will typically require a smaller rod to prevent excessive heat buildup and warping of the metal.
- Current type and amperage: The type of current used in the welding process (AC or DC) and the amperage of the current also affect the appropriate rod size. Generally, higher amperage will require a larger rod, while lower amperage will require a smaller rod.
- Material being welded: The type of material being welded (steel, aluminum, etc.) can also affect the appropriate rod size. Each material has its own specific welding rods designed for that material.
It is always a good practice to consult the welding rod manufacturer’s recommendations and follow the welding procedure specified by the welding codes.
Check out the Detailed information for Stainless Steel Rods.
What do the numbers mean on welding rods?
Welding rods have numbers printed on them that indicate their composition, tensile strength, and other characteristics. These numbers are known as the American Welding Society (AWS) classification or AWS electrode classification.
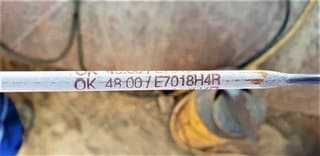
The AWS classification system for welding rods uses a series of letters and numbers to indicate the type of electrode, the type of coating, the welding position, and the minimum tensile strength.
The numbers on welding rods indicate the AWS classification and refer to the composition, tensile strength, and other characteristics of the electrode. The first two characters indicate the electrode welding strength, followed by digits indicating the welding position, and welding rod features.
For example, E6010, E6011, E6013, E7014, E7024, etc. are the welding rods classification numbers. Their meaning will be:
- E stands for electrode.
- The first two digits indicate the minimum tensile strength in Ksi of the weld metal.
- The third digit indicates the position in which the electrode can be used.
- The fourth digit is a filler metal type indicator.
For example, an E6011 electrode has a minimum tensile strength of 60,000 psi, can be used in all positions, and is an all-position electrode with a cellulose-potassium coating.
An E7014 electrode, on the other hand, has a minimum tensile strength of 70,000 psi, can be used in all positions, and is an all-position electrode with a high iron powder titania coating.
Complete welding electrode numbers and their coating types, welding positions they can be used and type of welding current are given in the below table (Reference: AWS A5.1 Specification).

It is important to match the electrode number to the type of welding and the type of metal being welded.
Welding rod sizes chart
Welding rod sizes and recommended welding amperage chart is given below for reference. The actual values may vary based on welding position and material thickness.
Welding Rod Size | Diameter (inches) | Diameter (mm) | Recommended Amperage |
1/16 | 0.0625 | 1.6 | 40-80 |
3/32 | 0.09375 | 2.4 | 80-120 |
1/8 | 0.125 | 3.2 | 80-150 |
5/32 | 0.15625 | 4.0 | 110-180 |
3/16 | 0.1875 | 4.8 | 130-210 |
7/32 | 0.21875 | 5.6 | 150-240 |
1/4 | 0.25 | 6.4 | 170-270 |
How do I know what size welding rod I need?
Choosing the correct size welding rod depends on several factors including:
- Type of welding process.
- Thickness of metal.
- Welding position.
- Type of metal.
- Current type and amperage.
- Welding rod manufacturer’s recommendations.
- Welding procedure (WPS).
E6010 Welding Rod size and Amperage Chart
Here is a table showing the recommended welding rod sizes and amperage for E6010 welding rods:
Welding Rod Size | Recommended Amperage (DCRP) |
3/32 | 40-90 |
1/8 | 60-110 |
5/32 | 80-130 |
3/16 | 100-160 |
E6011 Welding Rod size and Amperage Chart
Here is a table showing the recommended welding rod sizes and amperage for E6011 welding rods:
Welding Rod Size | Recommended Amperage (DCRP) | Recommended Amperage (AC) |
3/32 | 40-90 | 40-80 |
1/8 | 60-120 | 60-110 |
5/32 | 110-150 | 90-140 |
E6012 Welding Rod size and Amperage Chart
welding rod sizes and amperage for E6012 welding rods:
Welding Rod Size | Recommended Amperage (DCEN) | Recommended Amperage (AC) |
3/32 | 50-80 | 50-80 |
1/8 | 80-120 | 80-100 |
5/32 | 130-190 | 90-150 |
3/16 | 170-240 | 130-200 |
E6013 Welding Rod size and Amperage Chart
welding rod sizes and amperage for E6013 welding rods:
Welding Rod Size | Recommended Amperage (DCEN/ DCEP) | Recommended Amperage (AC) |
3/32 | 70-110 | 70-120 |
1/8 | 100-130 | 110-140 |
5/32 | 130-180 | 150-190 |
3/16 | 170-240 | 190-250 |
E7014 Welding Rod size and Amperage Chart
welding rod sizes and amperage for E7014 welding rods:
Welding Rod Size | Recommended Amperage (DCEN/ DCEP) | Recommended Amperage (AC) |
3/32 | 70-110 | 80-100 |
1/8 | 100-140 | 110-140 |
5/32 | 135-190 | 130-200 |
3/16 | 170-235 | 180-240 |
What size is a 7018 welding rod?
7018 welding rod sizes are 3/32, 1/8, 5/32 and 3/16 inches.
What size is a 6013 welding rod?
6013 welding rod sizes are 3/32, 1/8, 5/32 and 3/16 inches.