What is Polarity in Welding
Welding Polarity is the electrical circuit that is created when we turn on the welding machine (DC type) having a negative and a positive pole. Polarity is an important factor in the selection of the welding process for different materials. E.g, using AC polarity in TIG Welding for Aluminum Welding.
It is an important parameter for Stick Welding where different welding electrodes require different welding polarities for good welding results. Choosing the right polarity affects the appearance, strength, and quality of the weld.
A wrong polarity selection will result in high spatters, insufficient or excessive penetration, & a lack of control of your welding arc.
Types of Welding Polarity/ Current in SMAW, GTAW, FCAW & GMAW
The three different types of current or polarity used for welding are:
- Alternating current (AC),
- Direct-current electrode negative (DCEN) is also called straight Polarity.
- Direct current electrode positive is also called DCEP and Reverse Polarity.
What is Direct Current Electrode Negative or DCEN Polarity?
DCEN or also known as Straight Polarity works with the electrode connected to the negative, and the work is connected to the positive terminal as shown in the below picture (left side).
The electrons flow from the Cathode (Welding electrode) to the Anode (workpiece). This gives around 1/3 of the welding heat on the welding rod and 2/3 on the base material being welded. Straight polarity due to the above reason results in high welding rod melting.

DCEN is used in GTAW/ TIG welding as well as some limited applications in Shielded metal arc welding (Stick Welding).
DCEP heats the electrode much more than DCEN in TIG welding; thus, DCEP is rarely used in the TIG Welding process.
What is Direct Current Electrode Positive or DCEP Polarity?
DCEP is also called Reverse Polarity. In DCEP as you can see in the above picture- the job is connected to the negative terminal and the welding rod is connected to the positive terminal.
The electrons flow from the base material to the welding rod (cathode to anode flow of electrons). Change in these terminal points as stated above results in 2/3 heat concentration on the welding rod and 1/3 on the base material to be welded.
DCEP is used in Stick Welding (SMAW), GMAW (MIG/MAG, FCAW), and SAW welding processes. Due to high heat at the electrode end, DCEP results in a higher melt-off of the filler wire or electrode thus yielding in higher weld deposit compared to DCEN.
What is DCEP and DCEN in welding?
DCEP and DCEN welding are two different types of welding that use different methods to create a weld. DCEP welding, or Direct Current Electrode Positive (also called Reverse polarity), uses a direct current to create an arc between the electrode (connected to the Positive terminal) and the workpiece (connected to the Negative terminal).
This type of welding is often used in Stick Welding (SMAW), GMAW (MIG/MAG, FCAW), and SAW welding processes.
DCEN welding, or direct current electrode negative (also called Straight Polarity), also uses a Direct Current to create an arc between the electrode (connected to the Negative terminal) and the workpiece (connected to the Positive terminal).
DCEN is mainly used with some type of Stick Welding electrodes. In TIG welding, DCEN is mainly used as it produces less heat on the non-consumable tungsten electrode, thus improving its working life.
What is Alternating Current (AC) Polarity?
Alternating Current (AC) polarity uses alternating current and hence there are no negative or positive terminals. The electron flows keep alternating every 1/120 seconds from the welding rod to the base material. AC polarity with alternating terminals brings cleaning action to the workpiece.
This action is highly beneficial for welding materials having tough oxide layers such as aluminum & magnesium alloys welding.

How do you determine the polarity of a weld?
The polarity of a weld is determined by the direction of the current flow. In a weld, the electrode is the positive terminal, and the workpiece is the negative terminal. The polarity can be reversed by changing the leads on the welding machine, which changes the direction of the current flow. Reversing the polarity will change the appearance of the weld puddle.
Effect of Welding Polarity on Penetration & Heat Distribution in Welding
In GMAW, if we keep the electrode negative, the arc will become unstable, and the spatter is excessive as well as less heat on the welding wire, thus low melt-off rate. Similarly, in GTAW, if we keep the tungsten electrode positive, it will lead to the melting of the tungsten electrode fast.
This can cause tungsten inclusion in the weld as well as other welding defects. Thus, a correct selection of the welding polarity is very important. The effect of welding polarity and heat distribution is shown in the below figure.
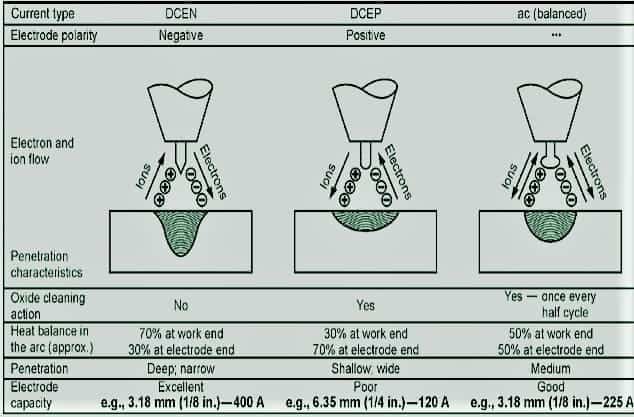
Stick Welding Polarity
Stick welding is a welding process that uses a consumable electrode to create the weld. The electrode is a piece of metal that is connected to the workpiece and melted by the arc.
Following are the types of stick welding polarities:
- Direct current (DC) and
- Alternating current (AC).
The type of current used will determine the polarity of the electrode. In Direct Current, the way of connecting the electrode holder to the machine defines further welding polarity in two types:
- DCEP: Direct Current Electrode Positive
- DCEN: Direct Current Electrode Negative
The direct current produces a straight, or constant, flow of electricity. The direct current produces a negative or positive polarity, as explained above.
The alternating current (AC) produces a wave-like flow of electricity. This type of current is used to weld metals such as Aluminium & Magnesium that require cleaning action to clean surface oxide layers.
Mig Welding Polarity
Mig welding is a common welding process that uses a consumable wire electrode to create a weld. The electrode is fed into the weld joint from a spool, and the welder directs the welding arc between the electrode and the workpiece.
There are two types of mig welding polarity:
- Direct current (dc), mainly DCEP is used in MIG-MAG Welding applications.
- Alternating Current (ac)., AC Polarity is used for Aluminum MIG Welding & in Tandem MIG Process.
Welding with gmaw utilizes the polarity as DCEP (Electrode positive) also called, Reverse Polarity. Here, the gmaw torch (wire feeder) is attached to the positive terminal and workpiece is connected with the negative point on the welder.
Flux Core Welding Polarity
When welding with Flux Core Arc Welding (FCAW), the polarity of the welder can be either DC (direct current) or AC (alternating current). In DC mode, the electrode is always positive, and the workpiece is always negative. This creates a more stable arc and produces less spatter.
In AC mode, the polarity alternates between positive and negative, which creates a more stable arc and produces less spatter. Most flux core welders operate in DC mode, but some can be switched to AC mode.
TIG Welding Polarity
In welding, the polarity of a power source determines the direction of electron flow. In TIG welding, the electrode is always the negative terminal and the workpiece is always the positive terminal.
The reason- there is less heat in the negative which in turn is beneficial for a long life of non-consumable Tungsten electrodes in TIG welding. If Tungsten is made Positive (DCEP), there will be high heat on the tungsten electrode and it will get damaged very frequently, thus reducing its life.
The polarity of a TIG welding machine can be changed by reversing the leads on the power cord. When the machine is set to reverse polarity, current will flow from the workpiece to the electrode instead of from the electrode to the workpiece. When Welding Aluminum, AC polarity is used in TIG Welding applications.
Welding Polarity Chart
Welding polarity is the direction of electrical current flow through a welding circuit. The most common type of welding polarity is direct current (DC), which flows in one direction.
Read more: AC vs DC Welding.
Alternating current (AC) also flows in one direction, but it reverses its flow many times per second. Welding Polarity Chartis is useful to decide the welding polarity for different stick welding electrodes.
With the help of a polarity chart, the welder can directly choose the welding polarity based on the welding electrode type. Below is an example of Stick Welding electrode Polarity Chart.

There are two types of DC welding polarity: straight polarity and reverse polarity. In straight polarity, the positive electrode (the wire or stick that’s melting the metal) is attached to the negative terminal of the power supply.
In reverse polarity, the positive electrode is attached to the positive terminal of the power supply. The below Welding Polarity Chart includes welding polarity for MIG, TIG & Stick Welding applications.

Most welders use direct current with a straight polarity setting for most welding applications. However, reverse polarity can be useful for certain types of welding, such as TIG welding aluminum.
Aluminum Mig Welding Polarity
in MIG Welding (GMAW) of Aluminum AC Polarity is used. AC Polarity gives cleaning action for aluminum MIG Welding enabling a good welding quality along with oxide cleaning action. Pure argon or helium as a welding shielding gas is used for MIG welding of Aluminum.
which dc polarity is most commonly used in mig welding due to it’s stable arc, low spatter, good weld bead characteristics, and greatest depth of penetration for the widest range of amperages?
Similar Posts: